ものづくりの現場とTPM
製造現場の役割、それはひと言でいうと「お客さまが必要とする量の製品を、必要とするときまでに、すべて良品であることを保証して、安い価格で提供する」ことでしょう。では、その役割が果たせずに困っている実情とはどのようなことなのでしょう。
- 突然設備が故障して、生産計画が守れない
- 段取り替えがやりにくく、調整にも時間がかかる
- 手直し品が多いので、頻繁に品質チェックをしなければならない
- 設備がチョコチョコ止まるので、見回りが大変だ
これらはすべて「安心して設備を使える状態」でないために、右往左往させられているといえるかもしれません。
また、
- やりにくい作業が多く、注意してもときどき失敗してしまう
- 作業バランスが悪く、自分だけが一生懸命仕事をしているように感じる
- 一日中歩き回っている
- やっている作業がムダではないかと思ってしまう
というように「ラクに安心して作業できない状態」だと感じていませんか? さらに、
- 油の飛散などで作業服が汚れやすく、すべって転びそうになる
- 治工具などの整理・整頓ができておらず、探す時間が長い
- 仕事をしていて、ヒヤリとしたりハッとしたりすることがある
- 夏は暑く、冬は寒い
- 力のいる作業が多く、騒音がうるさい
というように「働きやすい職場とはいえない状態」だといえませんか?
このように、いま困っている状態、たとえば安心して設備を使えない状態、ラクに安心して作業できない状態、働きやすい職場とはいえない状態などを自分たちの小集団活動で改善して「会社の業績に貢献できる」ようになることが、TPM、さらには自主保全のねらいであるのです。
TPMの定義
TPMとは、全員参加の生産保全(Total Productive Maintenance)と全員参加の生産経営(Total Production Management)の頭文字から成り立っています。設備の効率化は当然のこと、生産システム全体の効率化の極限追求を図り、企業の業績向上や参画型経営を実現する全員参加の企業体質改善活動です。
TPMの定義は、5つの項目から構成され、それぞれ以下のようなことを標榜しています。
TPMとは、
①生産システム効率化の極限追求(総合的効率化)をする企業体質づくりを目標にして、
②生産システムのライフサイクル全体を対象とした「災害ゼロ、不良ゼロ、故障ゼロ」など、あらゆるロスを未然防止する仕組みを現場・現物で構築し、
③生産部門をはじめ、開発・営業・管理などのあらゆる部門にわたって、
④トップから第一線従業員に至るまで全員が参加し、
⑤重複小集団活動により、ロスゼロを達成する
ことをいう。
①:TPMの目標
②:目標を達成する手段
③~⑤:誰が主役となり活動に取り組むのか
TPMの目的とは「生産システム効率化を図り、儲ける企業体質をつくること」、その手段とは「生産システムに潜在するあらゆるロスをゼロにすること」、さらに「ロスゼロはあらゆる部門が全員参加で取り組むこと」、これがTPMです。
単にロスを削減する活動ではありません。ロスやムダを減らす活動ならばほかにもあるのでしょうが、TPMは削減だけでなく、発生させない予防(保全)の仕組みを現場現物で構築します。これがTPMの大きな特徴なのです。
TPMの本質
TPMは、あくまでも企業が利益を生み出す儲ける技術・手段です。活動自体が目的になってはなりません。
期待どおりの結果(利益)をもたらす儲ける仕事のやり方とその質の向上を図り、単なるテーマ改善活動にとどまらない、仕事そのものを再構成する活動、これがTPMなのです。
儲ける仕事のやり方のヒントは、基本理念の2番目「予防哲学(未然防止)」にあります。故障や不良といったロスをゼロにすることで儲かる、TPMはこう考えています。ロスゼロを達成するには、「ロスを減らす」だけでなく、「ロスを防ぐ」「未然防止する」仕事のやり方が必要なのです。
あらゆるロスを把握してゼロに
TPMは、生産システムに潜在するあらゆるロスを把握してゼロにすることで、企業利益の拡大と儲ける企業体質を実現する活動です。生産部門に限らず、受注から納品までのビジネスプロセス全体を対象としています。
TPMでは、生産システムに潜在するロスは、生産を中心とした16大ロスを基本としています。では、どのようなロスがあるのでしょうか。
16大ロスを大きく区分すると、 ① 設備の効率化を阻害する8大ロス、 ② 人の効率化を阻害する5大ロス、 ③ 原単位の効率化を阻害する3大ロスに分かれます。TPMでは、まずこれらのロスを定量的に把握します。そして、ロスを「減らす」活動と「防ぐ」活動を役割分担して、関係者全員でロスゼロを達成します。
TPM活動の柱
TPMでは、16大ロスゼロを達成するために、8つの活動を全員参加で取り組みます。これを「TPM展開の8本柱」といいます。ロスを「減らす」活動とロスを「防ぐ」活動を分類すると、8本柱の活動に整理されます。
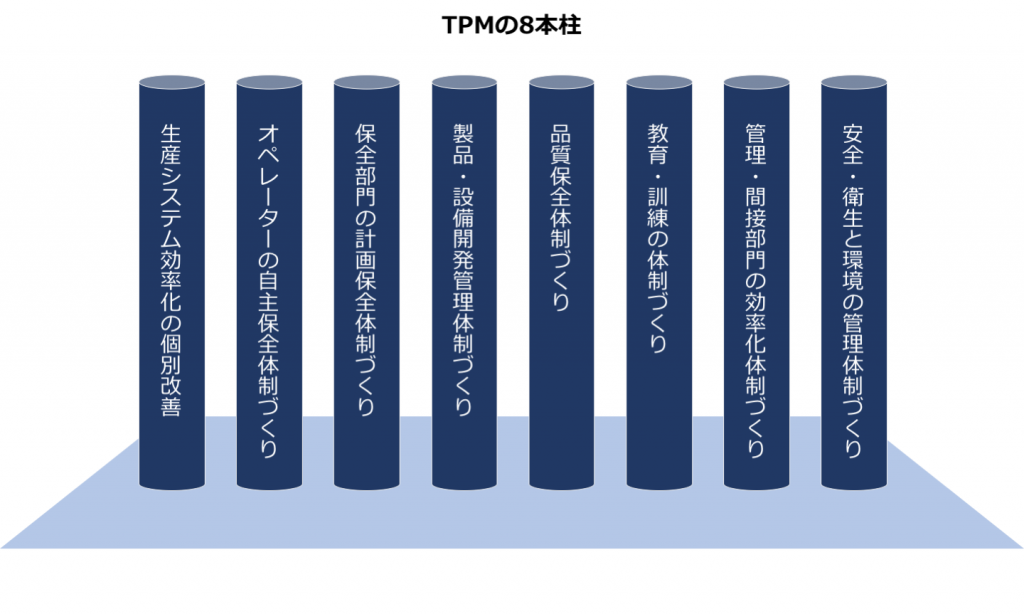
①生産システム効率化の個別改善
生産ライン(プロセス)や設備ごとにロスを調査・定量化して、ロスを減らし「真の儲け」を得る活動です。
②オペレーターの自主保全体制づくり
ロスを防ぐ代表的な活動であり、自分の設備は自分で守る自主自律体質を築くことをねらいとしています。
③保全部門の計画保全体制づくり
設備の劣化診断と復元、さらに改良保全による寿命延長を行い、故障ゼロと保全費低減を図る保全部門の活動です。
④製品・設備開発管理体制づくり
製品や設備の開発・設計段階に、生産時に発生が予想されるロスを防ぎ、垂直立上げを図る活動です。
⑤品質保全体制づくり
不良の出ない条件設定とその維持管理、さらに不良の発生の可能性を予知して事前に対策する、不良ロスを防ぐ活動です。
⑥教育・訓練体制づくり
仕事を進める上で必要な知識や技能を整理し、ロスを減らす・防ぐためのスキルアップを図る活動です。
⑦管理・間接部門の効率化体制づくり
生産現場のロスを減らす・防ぐ活動を支援するとともに、自部門においても同様の活動を行います。
⑧安全・衛生と環境の管理体制づくり
災害ゼロ・公害ゼロ・ゴミゼロ、さらに快適職場の実現をねらう活動です。
8本柱の活動においては、各活動は連携プレーで成り立っている点もTPMの特色となっています。
自主保全の7ステップ
TPM活動の大きな特徴でもある自主保全は、以下の7つのステップに沿って活動します。
①第1ステップ:初期清掃
設備を清掃することにより、汚れによるストレスを排除するとともに、不具合(漏れ・ゆるみ・損傷など)を発見し、発見したものは復元します。
その際、発見した不具合の個所に、不具合の内容、日時、発見者などを記入した札(エフ)を取り付け、復元が完了すればそれを取り外します。この不具合の発見をエフ付け活動、その復元をエフ取り活動といいます。
これらを通じて設備の機構を理解するとともに、不具合を不具合として見る目を養います。また、「清掃は点検なり、点検は不具合の発見なり、不具合は復元改善するものなり、復元は成果なり、成果は喜びなり、喜びは次への糧なり」を体験します。
②第2ステップ:発生源・困難個所対策
ゴミ・汚れの発生源を断ち、飛散防止や清掃・給油の困難個所を改善し、与えられた目標時間で清掃・給油ができるようにします。また、改善を通して「改善の目を育てる」、つまり観察・解析・対策を行うことによって改善の4原則であるECRSを学ぶことになります。何度も改善を重ねることによって、設備に対する愛着が生まれてくるのです。
③第3ステップ:自主保全仮基準の作成
第1・2ステップを継続して維持するために、清掃仮基準の作成と、給油と潤滑状態を見直し、不具合個所や給油・点検困難個所を摘出・改善して仮基準を作成します。このことによって、設備の信頼性と保全性の向上を図り、守りやすい基準書をオペレーター自らが作成します。この段階で、強制劣化のない姿にし、維持を行います。
④第4ステップ:総点検
設備の極限効率化を図るために、設備、部品に至るまでの構造・機能・原理の理解と「あるべき姿」を学び、設備を漏れなく点検し、潜在化している欠陥を顕在化して本来の姿に復元・改善します。
締結、潤滑、油圧、空圧、駆動、電気、安全、加工条件などすべてが対象となり、この段階であるべき姿の知識と、点検・復元技能を持つことになり、設備に強いオペレーターが育成されることになります。
⑤第5ステップ:自主点検
第1~4ステップで実現した設備の劣化・復元状態をこれからも維持・改善し、設備の信頼性・保全性・設備品質をさらに高めなければなりません。そのために、これまでに作成した清掃・給油・総点検・設備品質点検それぞれの基準を見直します。このように点検の効率化と点検ミスのない状態をつくりあげ、自主保全基準(第3ステップが仮基準であるのに対して、ここでは本基準)をまとめあげて実践します。
保全部門の年間保全カレンダーとの突き合わせや、個別改善からの維持項目の見直しも行って、故障ゼロの設備をつくりあげます。
⑥第6ステップ:標準化
これまでは、設備も中心に基本条件の整備や日常点検に重点を置いた活動を行ってきました。ここでは、この維持・管理を確実にするとともに、オペレーターの役割を設備周辺の関連作業にまで拡大して、さらに徹底したロス低減を図って自主管理を仕上げる基盤を構築します。設備管理のほかに、安全と品質、治工具、予備品、資材、計測器、作業、工程、工事、環境、物流、生産管理など、モノづくりに必要な日常管理項目を対象に、守られ度の確認と向上、さらに守りやすくする改善を通して各種の標準化を行います。
⑦第7ステップ:自主管理の徹底
これまでの活動をすべて集約化して、設備を変え、人を変え、職場を変えて成果を出した実績をもとに限りなくチャレンジして、参加・連携・創造と感動を味わう場となります。
上位方針に沿って、いま私たちの職場でやらなければならないものは何かを理解し、自ら積極的に取り組んでいきます。PDCAのサイクルがキチンと回り、全員で目標に向かう生き生きした職場になります。
改善チームの役割
各職場の改善チーム(小集団サークル)は、作業責任を果たすことが大前提です。職場にあるさまざまな決め事と職場環境の整備(働きやすさ・守りやすさの追求)を通じて、維持管理が確実にできる体質をつくりあげます。
職場では1人ひとりが役割を分担しているので、チームとしての役割を果たさなければなりません。具体的には、自主保全のステップを確実に展開することです。
守るべき事柄には、多くの課題、問題点、不具合が潜んでいるものです。その事実を把握して、自分たちで処置・回復するだけでなく、関係部門、さらには上流・源流に向かってどれだけ伝えることができるか、この点が重要なのです。
さらに、個別改善を展開して、職場全体がレベルアップしなければなりません。具体的には、
●職場にどのようなロスがどれだけあるかを把握する
●上位方針に沿って、期間内にどれだけの課題を解決すべきか決められるようになる
●課題を短期間で解決して、目標を達成できる
までレベルアップすることです。
さらに、改善を進めることによって、要因分析力、改善実施能力、条件設定能力など、QCストーリーに従って改善を展開する実力を身につけます。
本文は「現場が主役のTPM」(JMAC)の付録部分を一部編集して掲載したものです。