シングル段取りへの挑戦【3/6】
段取り改善へのステップ(2・3ステップ)
2ステップ:改善目標の設定
段取り替えそのものは、付加価値を生み出さない「ロス」だといえます。ロスは徹底的に排除し、段取り替えをやらない「10分」にすることを考えてみましょう。
とはいえ、すぐに段取り時間を「10分」にするのはムリだと思います。そこで、まずは半減を目指しましょう。
まず、現状の段取り時間を半分にします。次の改善でさらに半分、その次の改善でさらに半分という段階式で進め、最終的にシングルにもっていくという繰返しの改善となります。
仮に現状の段取り替えが1時間かかっていても、半減を3回繰り返せば以下に示すように10分以内のシングルにもっていくことが可能です。
60分→30分→15分→7.5分
具体的な目標が決まれば、あとはそれに向かって何をすれば実現できるか改善案を考えていきます。
3ステップ:ムダ作業の排除
(1) ECRSで改善の発想を
改善案を検討する場合の原則として、ECRSがあります。それぞれの意味は次のとおりです。
・E(Eliminate):やめられないか(排除)
・C(Combine):組み合わせられないか(結合)
・R(Rearrange):入れ替えられないか(置換)
・S(Simplify):簡単にできないか(簡素化)
段取り改善のアイデアを検討する場合も、このECRSでの発想がポイントとなります。各ステップで活用していくので、覚えておいて損はないと思います。
(2) ムダ作業を徹底的に排除する
このステップでは、段取り替え作業の調査で発見したムダ作業に対し、まずは“やめられないか”(排除)の視点から改善案を検討し、徹底的な排除を狙います(図表-5)。
図表-5 3ステップの改善対象範囲
●POINT ムダ作業は、まず“E=やめられないか”を考える
① 探すムダの排除
「探すムダ」を排除するための基本的な考え方は「5S、3定、表示を徹底する」ことです。
5Sの中でも、「整理(いるものといらないものを区分する)・整頓(守りやすい状態になること)」を徹底することが不可欠であり、段取り作業を行いやすいように、身の回りの環境をつくることが重要になります。
3定とは、定位・定品・定量の略で、段取りに使用する物の置き方、置き場所についてきちんとルール化し、定数、定置管理をします。そして、表示でそれが何かを誰でもわかるようにします。
② 移動・運搬のムダの排除
「移動・運搬のムダ」は、「探すムダ」と対の関係にある場合も多いので、「探すムダ」を排除することにより、ある程度は削減できると思います。
治具・工具、部品の「移動・運搬」はそのつど行うのではなく、一度の運搬で済むように作業用工具や部品などを積み込んだ段取り専用台車を作成するのもよいでしょう。
交換・調整作業の際に発生する「移動・運搬のムダ」は、段取りが始まったら「設備から5歩以内で作業ができるようにするにはどうすればよいか」という視点で、作業や物の配置を見直していくとよいでしょう。
しかし、大型の設備やライン化された設備の場合は、どうしても回り込みの移動時間が増えてしまいます。そのような場合は、複数名で分かれて段取りを行うことを勧めます。単純に考えても、2人で分担して行えば作業時間は2分の1になります。
③ 他のムダの排除
「探すムダ」「移動・運搬のムダ」以外のムダ作業の排除も、着実に積み上げていくことが重要です。図表-6にムダ作業の例をあげておくので、ヒントにしてください。3ステップが終了した段階での段取り時間の推移は、図表-7になります。
図表-6 ムダ作業の例
図表-7 3ステップと段取り時間の推移
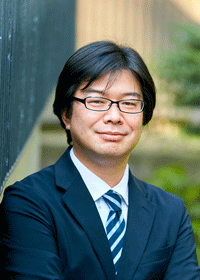
インテリジェントメンテナンスセンター
センター長 チーフ・コンサルタント
鐘ヶ江 克則(かねがえ かつのり)
大学卒業後、電気メーカーの生産技術者を経てJMACのコンサルタントに。生産戦略、生産方式、設備管理を専門領域とし、国内・海外の製造業において生産性改善、コストマネジメント、不良削減、在庫削減、リードタイム短縮など数多くのプロジェクトを支援。現在、高度設備保全技術の研究および設備保全業務のDXについて取り組んでおり、関係執筆も多数。