シングル段取りへの挑戦【5/6】
段取り改善へのステップ(5ステップ)
5ステップ:内段取り作業の効率化
ここまで改善を進めると、交換、調整作業といった必要な内段取りしか残っていないはずです。しかし、残っている内段取り作業の中には、まだまだ改善の余地があります。この段階で、すでに目標を達成した場合も多いかと思いますが、さらなる宝の発掘に取り組みましょう(図表-10)。
図表-10 5ステップの改善対象範囲
(1) 交換作業の効率化
交換作業の効率化は、取付け・取外し作業のすべてに対して簡易化を考えます。簡易化のポイントは着脱の改善です。
交換作業の簡易化の進め方は、現状の内段取りで行っている取付け・取外し作業の作業性、着脱において使用する工具・治具、締付け具1つひとつに対して、
・ボルトの本数を減らせないか
・ボルトやスパナを使わない締付け方法にできないか(レバー式クランプ、エアクランプ、油圧クランプなど)
・ボルト、工具の種類を減らせないか
・回り込み作業をなくせないか
・締結部の高さを統一できないか
といった視点で見ていき、改善案を抽出してください(事例-1)。
事例-1 交換作業の効率化の着眼点(締付け具)
簡易化のもう1つポイントは、作業分担と並行作業です。
大型設備やラインの交換作業では、前後、表裏、上下を動き回りながら作業をすることが少なくありません。そのような場合は、歩行のロス削減を考えて、複数人で作業配置分けをして作業を行うことも考えてみましょう。
また、1人で作業を行うより複数名で並行して行う方が、当然それに要する時間は短くなるので、内段取り作業そのものが短縮されます。並行作業とは、その効果をねらった作業方法です。
●POINT 交換作業の効率化は、着脱作業において“C=少なくできないか”、“S=簡単にできないか”と考える
(2) 調整作業の効率化
調整作業の効率化では、調整の排除を考えて進めていきます。
調整は、正確な基準設定を行っていないために発生する手直しや、やり直し作業です。それを逆に考えると、基準設定をきちんと行えば調整を排除できるということになります。
① 基準の統一
品種ごとに変わる寸法や位置、高さなどの基準を統一できないか検討します。すべての品種に対し、基準を合わせるのがむずかしいようであれば、ブロックやスペーサーを用いて一定にします(事例-2)。
事例-2 調整作業の効率化(基準の統一)
② 位置決めの改善
基準設定を整備したうえで、「突き当てガイド、ブロック、ピンなどを用いて、一発で位置決めできないか」「ワンタッチセットできないか」「目盛りを見る作業をなくせないか」などを検討します(事例-3)。
5ステップが終了した段階での段取り時間の推移が図表-11になります。
事例-3 調整作業の効率化(センター位置決めの改善)
図表-11 5ステップまでの段取り時間の推移
●POINT 調整作業の効率化は“E=調整の排除”と考える
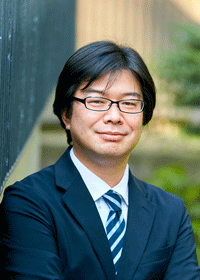
インテリジェントメンテナンスセンター
センター長 チーフ・コンサルタント
鐘ヶ江 克則(かねがえ かつのり)
大学卒業後、電気メーカーの生産技術者を経てJMACのコンサルタントに。生産戦略、生産方式、設備管理を専門領域とし、国内・海外の製造業において生産性改善、コストマネジメント、不良削減、在庫削減、リードタイム短縮など数多くのプロジェクトを支援。現在、高度設備保全技術の研究および設備保全業務のDXについて取り組んでおり、関係執筆も多数。