TPM鉄則37:改善の最大の目のつけどころは、現場に潜むロス
個別改善の主要な活動である「生産システム効率化」の目のつけどころは、現場に潜むロスです。ここではロスについて考えていきます。
ロスの分類
ロスは、正常に見える設備の中にも実はたくさん潜んでいます。そこで見えないロスを顕在化し、分類します。ロスは大きく分けて、①設備の効率化を阻害するロス、②人の効率化を阻害するロス、③原単価の効率化を阻害するロスに分類できます(シャットダウンなどを考慮する場合、操業度を阻害するロスが加わります)。
分類されたロスは、効率化の目的によって選択し、テーマ登録(名称、ロスの量、改善担当者・メンバー、終了日時など)をして、集中して改善に取り組みます。
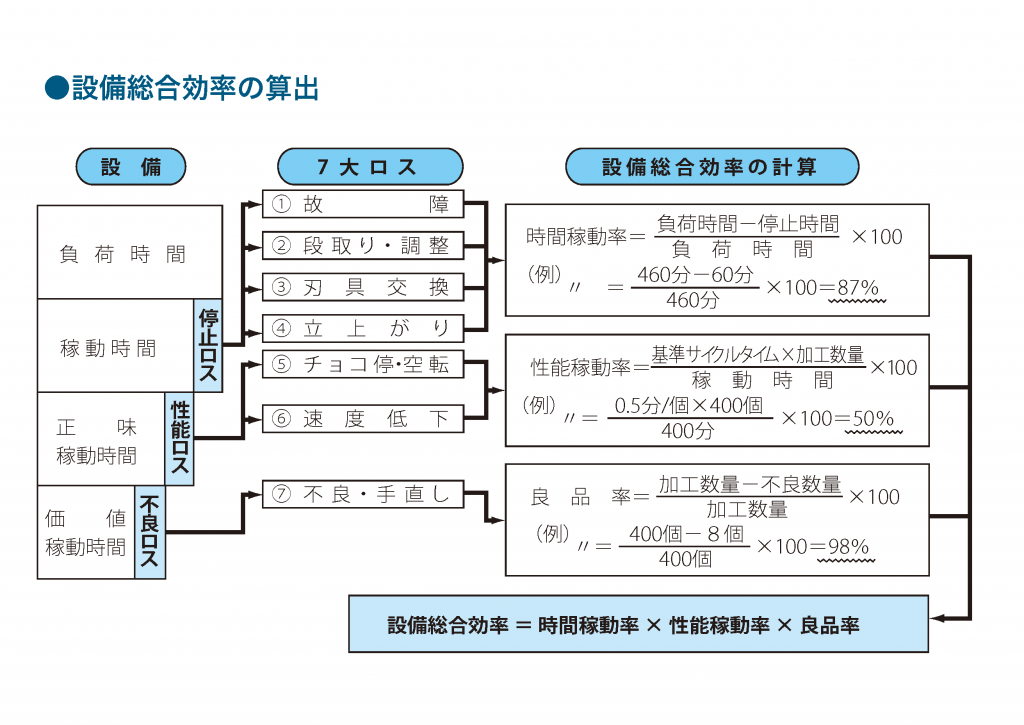
現場・現物でロスを顕在化する
個別改善では、組織の各階層の重複小集団のメンバー全員が、それぞれの役割ごとにテーマを決め、経済効果の極限を追求します。まず、生産システム全体を対象とした上記の大きなロスを、さらに細分化し16大ロスとして定義します。次に、事業実態に沿った大ロスを中ロスに分解し、これに相当するサブロスを現場で起こっている現実に沿って定義します。計測可能な単位および金額換算方法まで詳細な定義付けをしていきます。また、設備総合効率も計算します。
定義や計測方法などが決まったら、工程ごとにロスの現状を調査し、顕在化します。調査結果は、BM(ベンチマーク)としてすべて登録し、共有化を図り、ロスツリー、ロス―コストマトリックス、ロスマップなどを作成します。これらでロスの見える化を実施しま
す。管理帳票上のデスクワークでつかむロスでは、机上の空論で改善が進みません。ロスは、現場に潜んでいます。現場・現物で顕在化することが、現場が主役の活動において重要となります。
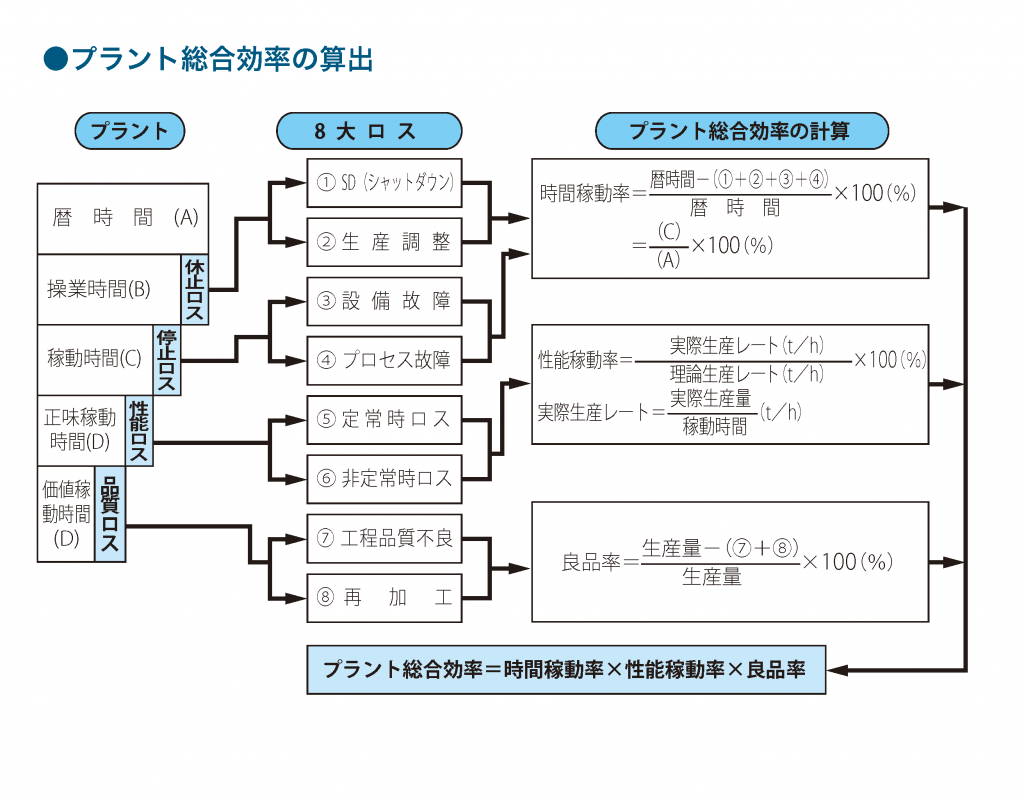