フクゲンとカイゼンと… 連載第8回
トラブルが起こると部品の形状や材質の変更などの改善を考えがちですが、新設設備は給油も十分ですし、ゴミや汚れもありません。ベルトも摩耗しておらず、設備はその機能を発揮して運転されています。このことは故障やトラブルは、部品の形状とか材質の問題ではなく、給油不足、部品の摩耗・腐食によって劣化し、その結果といえるのです。つまり、改善ではなく、まずは元の状態(あるべき姿)に戻すこと、すなわち復元が最高の設備効率を実現する早道である場合が多いのです。今月は、復元と改善の考え方と、オペレーターが取り組むべきことを紹介します。
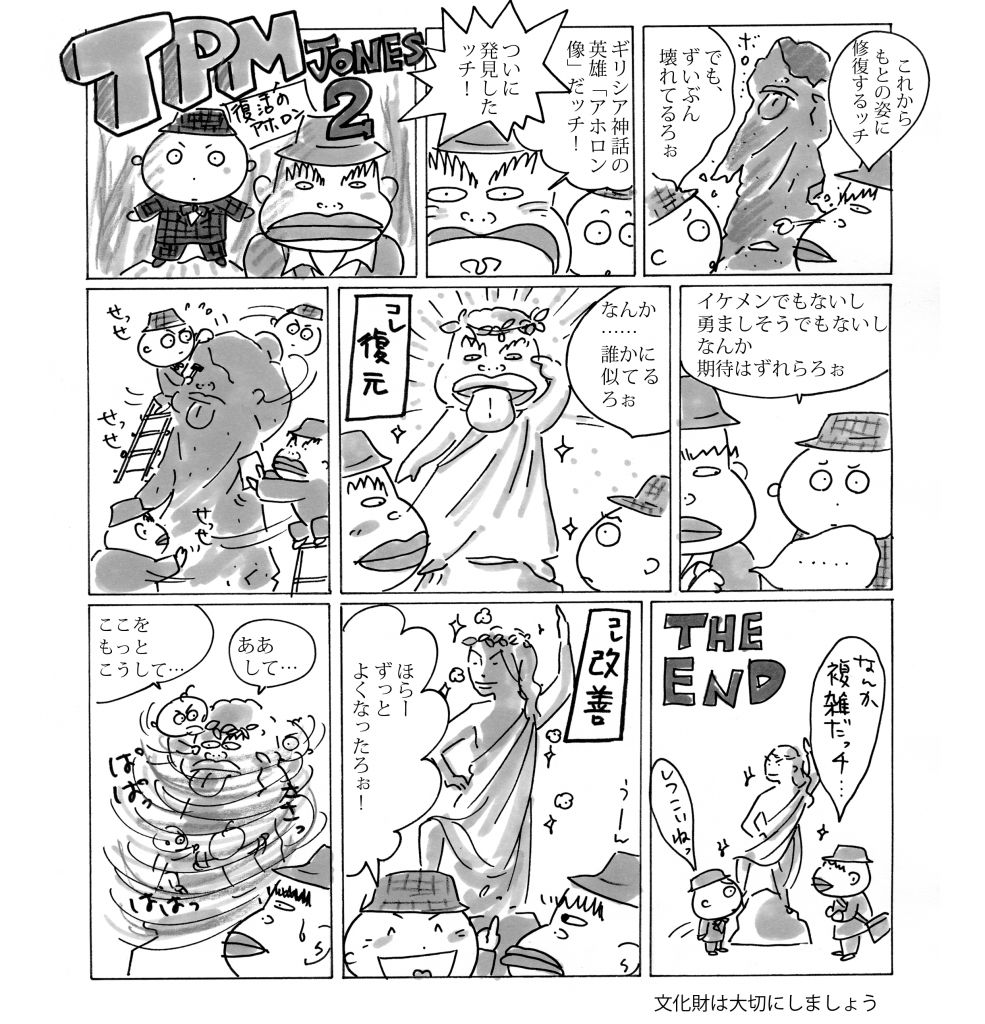
ここがポイント!
改善の前に復元を
生産現場で、私たちオペレーターがもっとも大きな影響を受けるのは故障です。その故障をゼロにするために、自主保全ではさまざまな活動を展開していきます。その1つが改善活動です。
改善活動は、復元と改善の内容を組み合わせた活動です。復元とは、「元の正しい姿に戻す」ことです。一般に故障が起きた場合、それを元の姿に戻す、つまり復元することによって、故障の大半をなくすことができるといわれています。
復元するためには、正しい状態から外れているものを見つけ出さなければなりません。そのために有効な方法が初期清掃です。徹底的に清掃することによって、設備の至る所にこびりついた長年のアカを落とし、変だなァ、おかしいなァという不具合点が数多く見つかります。つまり、設備本来の姿を点検することになるのです。
点検によって、
・ボルトのゆるみやガタはないか
・ベルトの張りはよいか
・切粉や切削油でモーターやポンプが汚れていないか
・油量や油の色はよいか
・タンクにゴミが入るようなすき間、穴がないか
・フィルターの目詰まりはないか
などの故障の原因が見つかります。
これらの対策はボルトの適正締付けやベルトを適正な張りにするなど、改善ではなく元の正しい姿に戻してやることで、故障削減にたいへん有効なのです。改善の前に復元です。
改善のポイント
徹底的に復元をしても故障が減らない、点検個所が多く時間内で点検が終わらない、清掃してもすぐ切粉や油で設備が汚れてしまう、ということがあります。このようなときに、改善を考えるのです。以下に改善のポイントの代表的なものをあげます。
(1) 透明カバーの設置
点検個所が設備のあちこちにバラバラにあったり、見えないカバーの中にあるような場合は、見えない個所を見えるように改善します。たとえば、ベルトの点検では、カバーの一部を透明なアクリル板にすることによって、ベルトの本数、摩耗の状態や汚れの程度、さらにテンションも調べることができます。
(2) 計器類を見やすく
設備についている計器類は、設備の後にあるものを前にもってくる、かがまなければ見えないものは目の高さで見える所にもってくるなどの改善を行います。これらの改善によって、点検時間を大幅に短縮することができます。
(3) 局所カバーは内製で
油や切粉の飛散対策には局所カバーを取付けることが有効なのは、みなさんもよくご存知でしょう。この際、カバーは自分たちが試行錯誤してつくることがポイントです。
(4) 集中給油方式と自動給油方式
給油個所が多い場合は、集中給油方式や自動給油方式などの改善が有効です。これは保全部門と相談しながら行うとよいでしょう。