「戦略的TPM」で新しいものづくり革新を―経営戦略とリンクする総合一貫型のTPMとは― No.11
第11回 S-TPMメニュー解説編 個別改善 S-TPMによる強化
個別改善 あらゆるロスの撲滅
■ロスゼロへの挑戦
個別改善とは、生産システムを効率化するにあたり、改善の対象を絞り込み「個別」に改善を重ねていくことです。設備や装置、プロセス全体について、徹底したロス排除と性能向上により最高の効率化を図り、改善テーマごとに階層別やプロジェクト活動でロスゼロに挑戦します。その考え方は、現場改善だけではなく企業活動全体にまで適用できます。
個別改善では、ロスを「あるべき姿」と「現状」の差と定義し、①現在発生(顕在化)しているロス、②潜在的に見えないロス、③将来発生してしまうロス--に焦点を当て、個別に撲滅していきます。個別改善以外のTPM活動は、ロスを発生させない予防活動と位置づけることができます。
個別改善を進めるには、まずは膨大なロスを発掘し、優先づけを行い、撲滅に取り組みます。標準的な進め方を図1に示しておきます。
図1 個別改善の進め方
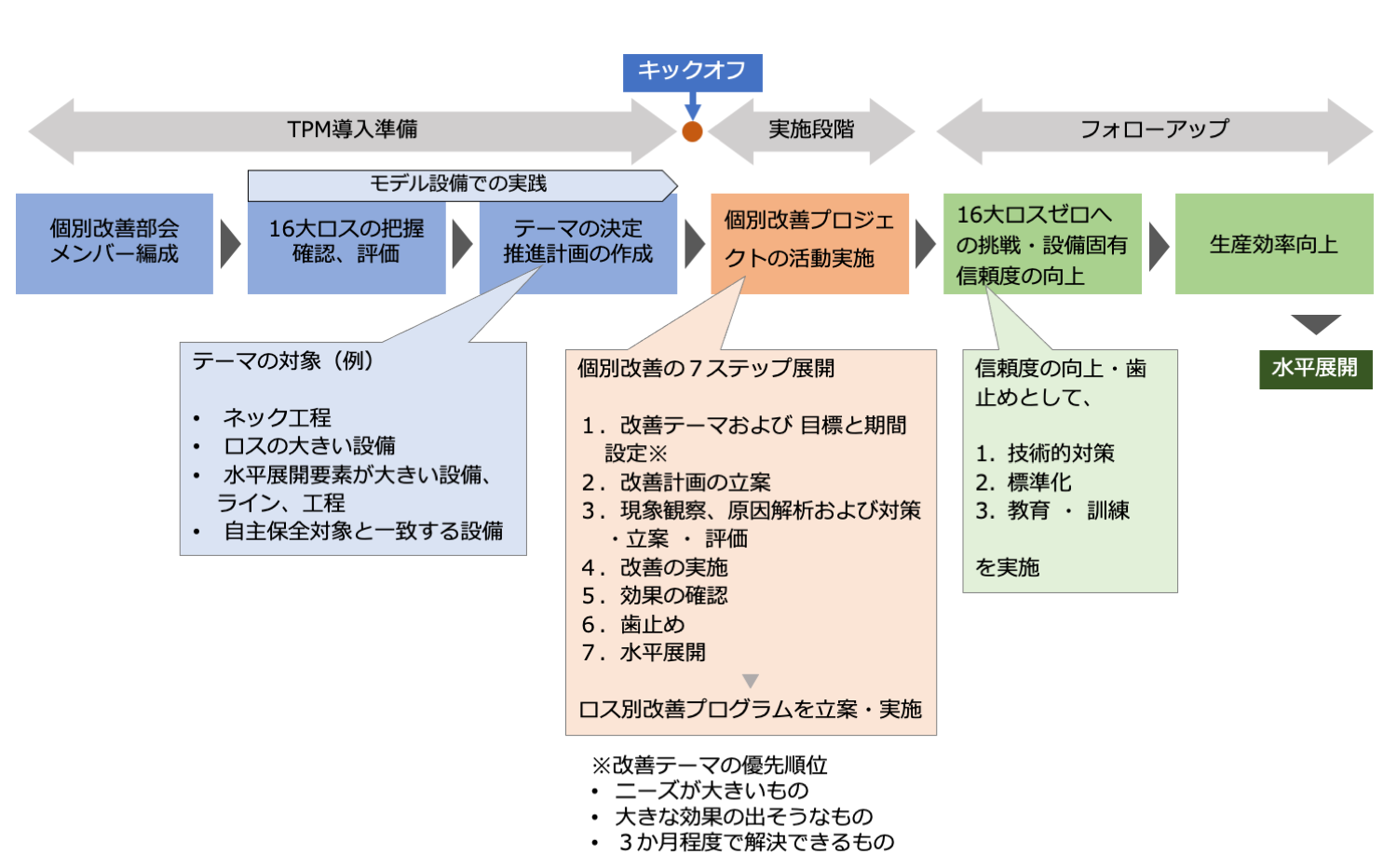
■ロスとコストを見える化する
生産システム効率化の最終的なねらいは、マン-マシンシステムの最高状態、極限状態を維持すること、すなわち設備の固有能力、人の能力を最高に発揮、維持することです。その結果として、付加価値生産性の増大、製造原価の低減などを操業度に影響なく達成することができます。
個別改善では効率化を阻害するロスを定義していますが、事業の形態や活動の進捗に応じて分類・設定することをお勧めします。JMACは16大ロスを例として提示しています(図2)。ロスはコストとの関係を明確にして、ロス撲滅のシナリオを作成することが大切です(図3)。
図2 生産活動におけるロス構造(16大ロスの例)
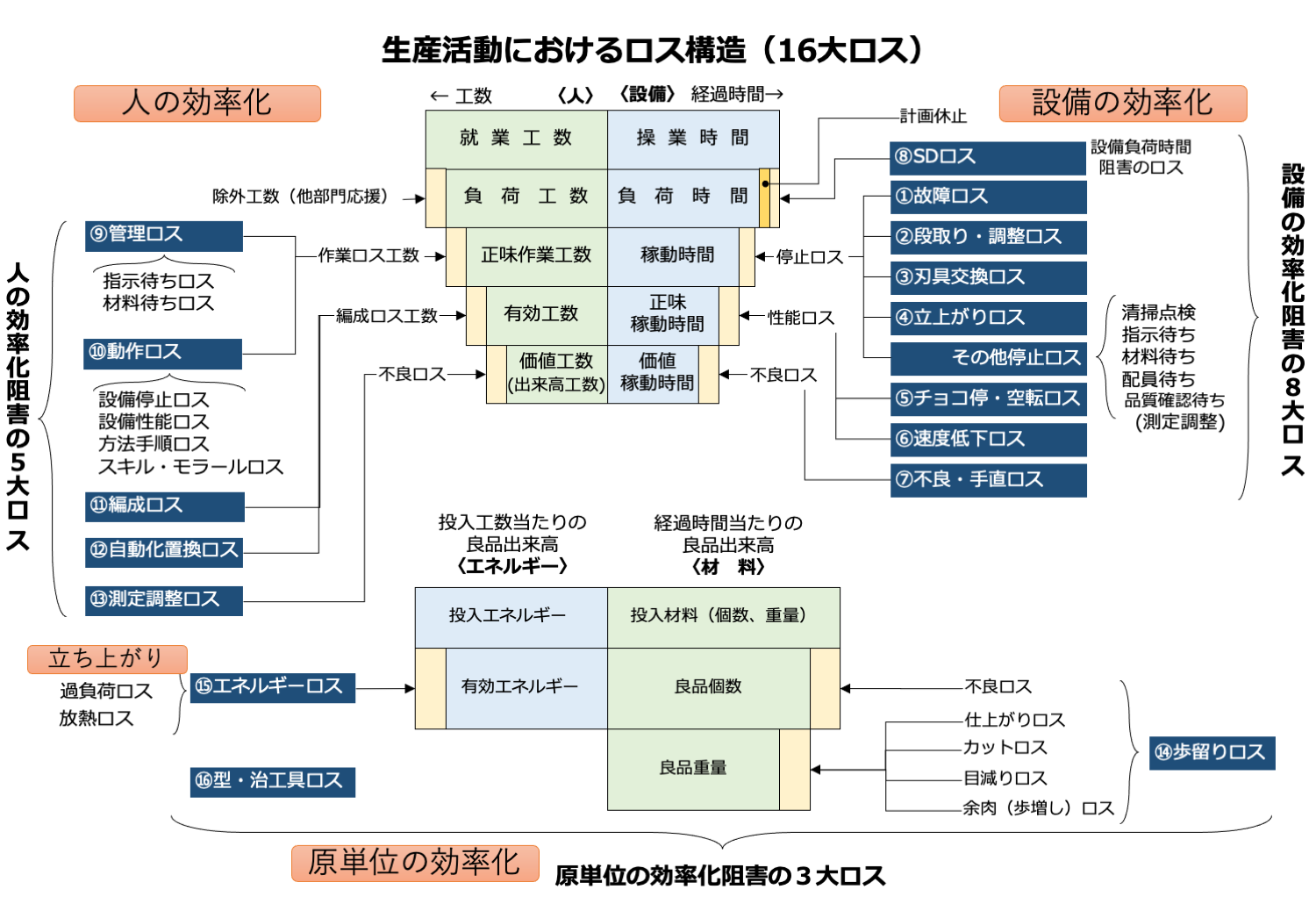
図3 コスト・ロス構造マトリックスの例
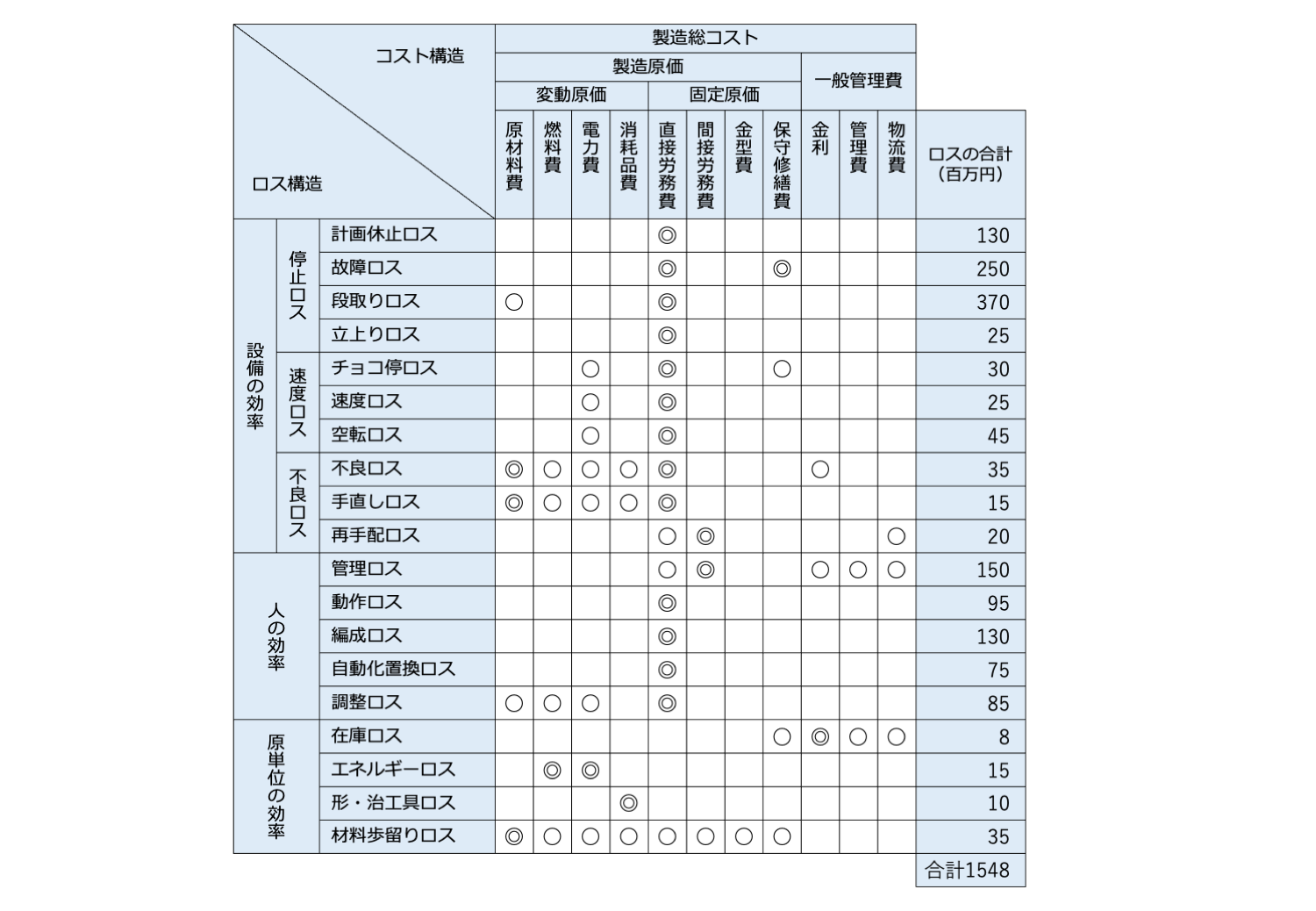
具体的な取り組みとしては、ネック工程分析、故障ゼロの改善プログラムなど、適切な手法を用いて進めます。さまざまな解析・分析手法、プログラムを十分に習得し、自主保全や計画保全、品質保全と連携して改善を進めていくのです。
一般的に、改善では結果に大きく寄与する要因を重点的に取り上げて対策を行います。しかし、慢性的に発生するロスの要因については、重点的にこれだと決めても必ずしも成果に結びつかないものも多いのです。ロスゼロを目指すのであれば、理屈で考えてロスに影響すると考えられる要因に対しては、重点にこだわらず、すべての要因に対策する必要があります。ゼロ志向のTPMでは重要な取り組みとなります。
図4は個別改善による活動目標を展開したもので、ロスツリーと呼ばれています。このように見える化しておけば、経営トップ、個別改善の分科会、TPM推進事務局とともに、プロジェクトや日々改善の推進管理を行うのに便利です。生産システム効率化のための改善が、いかに企業利益に貢献できるかを理解できるはずです。
図4 ロスツリーの例
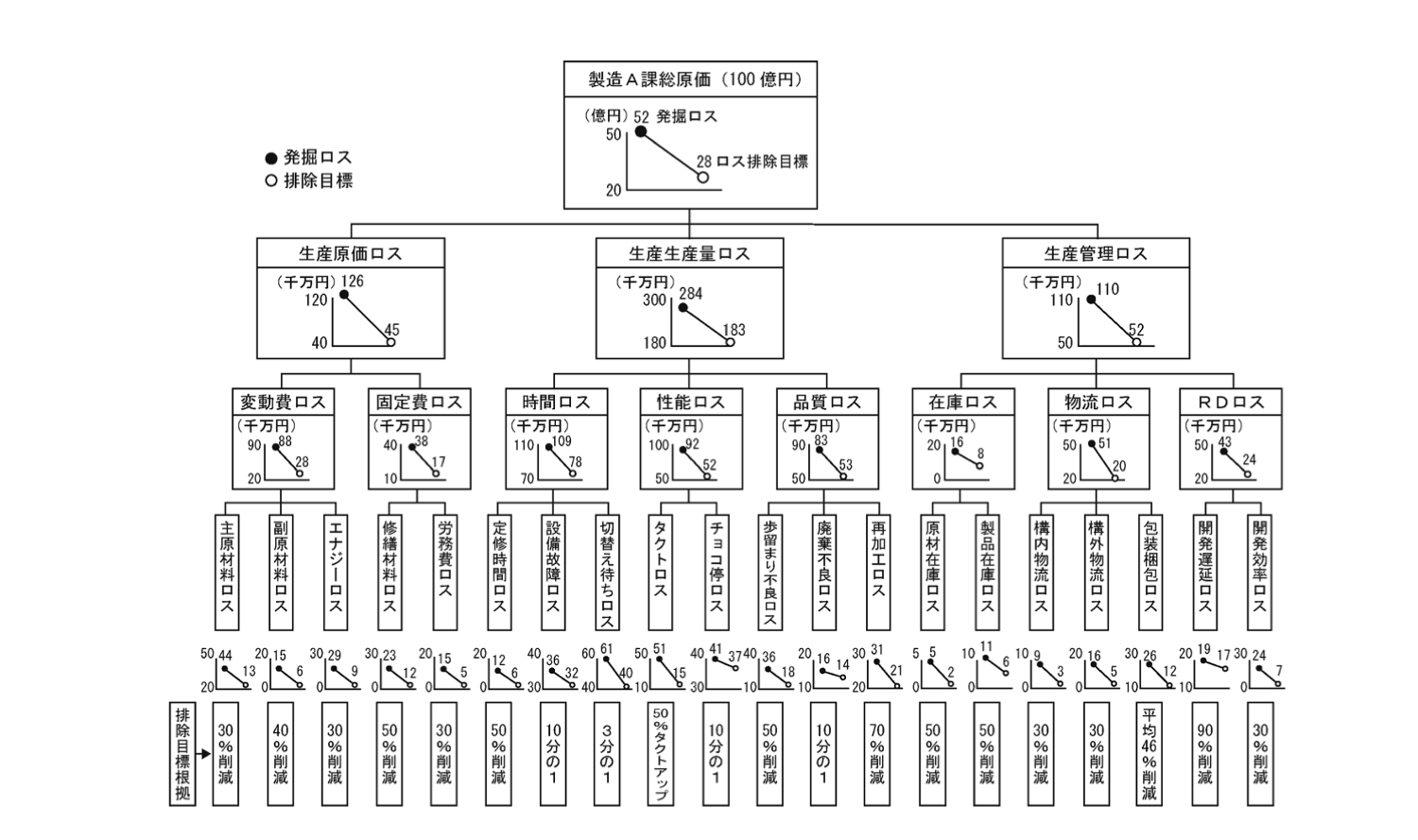
JMAC『TPMカレッジ管理者コース』テキストより
S-TPMで個別改善を強化
前回同様、個別改善についても近年の困りごととその対策方向およびS-TPMとしての強化事例を紹介します。
■個別改善の近年の困りごととその対策方向
図5は個別改善を取り巻く環境変化とその対応方向をまとめたものです。図では困りごととその対策方向を8つに分類しており、さらにグルーピングしてみると、①財務成果/成果、②改善人材・育成/指導方法/改善手法教育、③改善活動のつながり/目標・志/マネジメント--に大別できます。
総括すると、自主保全と同じように知恵のある賢い展開につまずいて、うまい展開ができていないと言えます。複雑な環境の中、コンサルタントや経営企画および経営者などの立場の人が、うまい展開を考える必要があります。
図5 個別改善を取り巻く環境変化とその主な対応方向
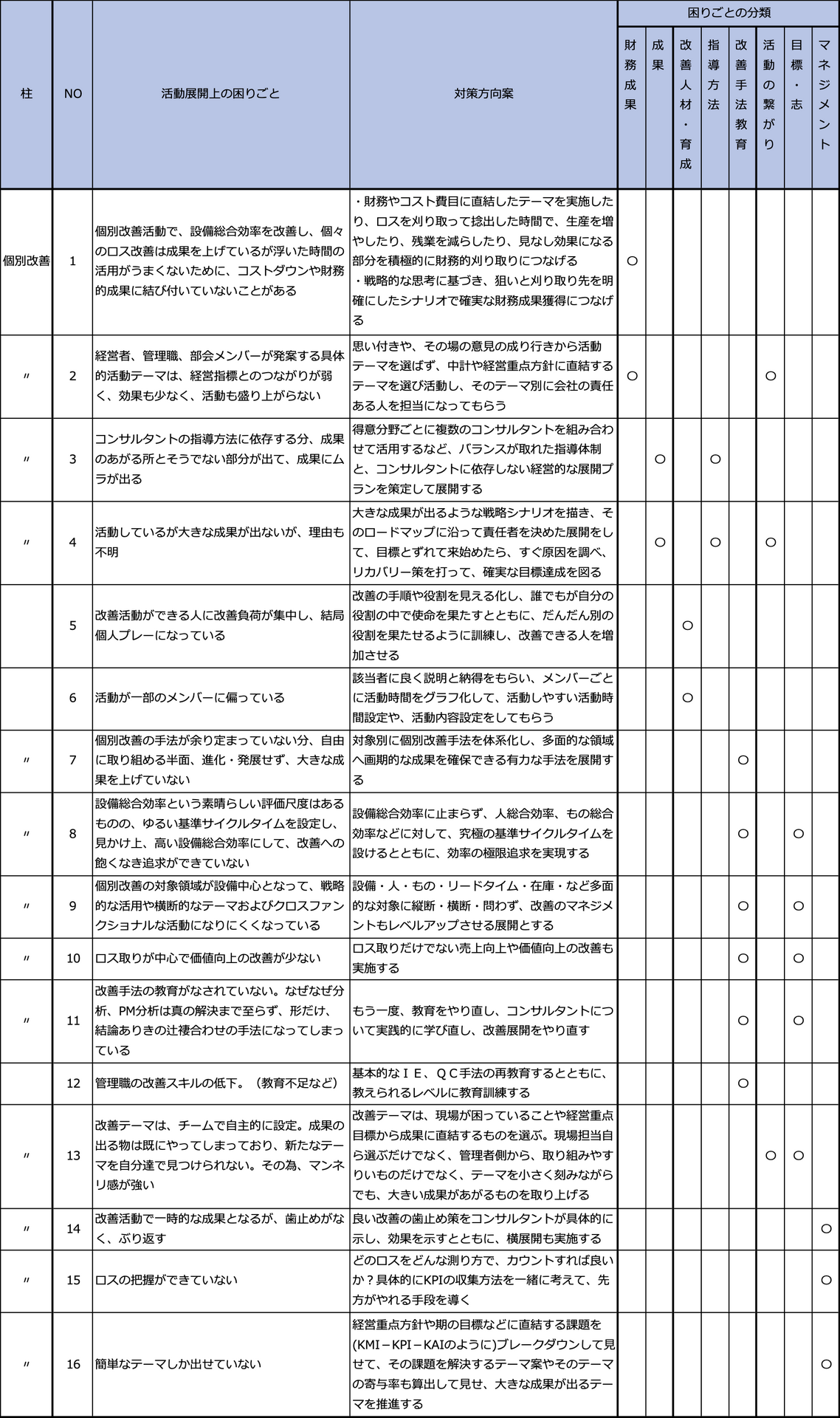
■S-TPMとしての個別改善の強化事例
従来の個別改善を強化していくための手順や考え方を以下で解説します。
①ロス削減から価値付加向上へ
従来の個別改善は、7大ロスの削減を中心に展開されている。それはそれで継続しながら、①価値稼動時間の見直し(設備生産性のn倍化)、②アウトプットの増大(図6)、③7大ロス以外の管理ロスや生産調整(仕事がないなど)ロスの削減をターゲットに展開します。
図6 ロス削減から価値付加向上へ
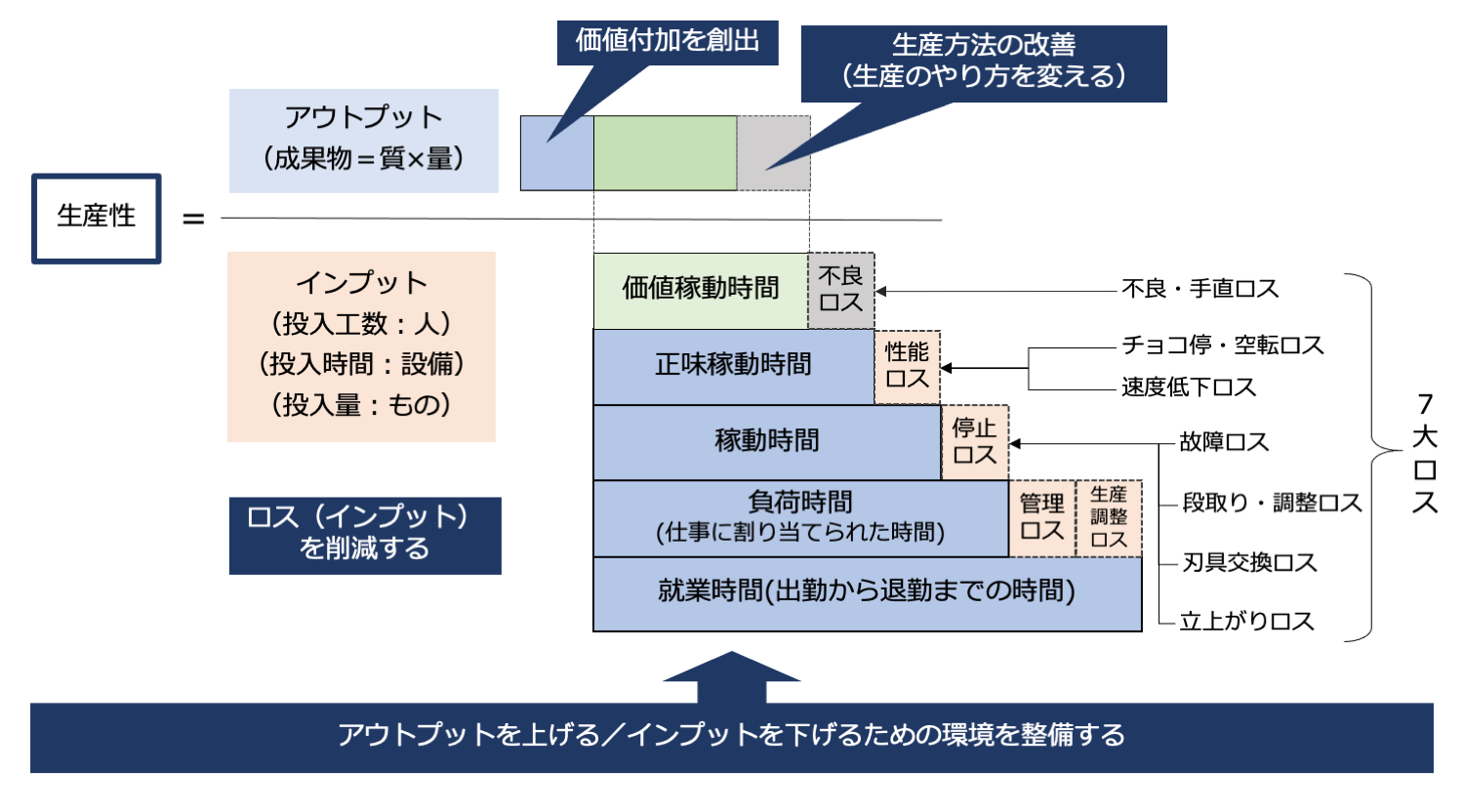
②基準・理論・理想への追求
極限追求のターゲット(目標)をレベルごとに設定することが大切です。
まずはレベル1です。当たり前のことを当たり前に、企業で決められている基準や標準スピードを常に実現する「基準の達成」が目標となります。
レベル2は現状の工法・設備方式を使う前提で、理論的に限界の極限値を目指す「理論の追求」です。
レベル3は現状の工法や製造方法にとらわれず、新しい工法やつくり方も含めて考案する理想的限界値に挑戦する「理想を目指す」レベル設定である。
以上を図式化して整理したものが図7です。設備やラインだけで挑戦する活動スコープ、工場全体で挑戦するスコープ、企業全体で挑戦するスコープ、さらには企業ネットワーク全体で挑戦するスコープと活動範囲を段階的に設定していき、最終的には企業ネットワーク(サプライチェーン全体など)の理想状態実現に向けて挑戦する目標が定まるということです。
図7 基準・理論・理想への追求
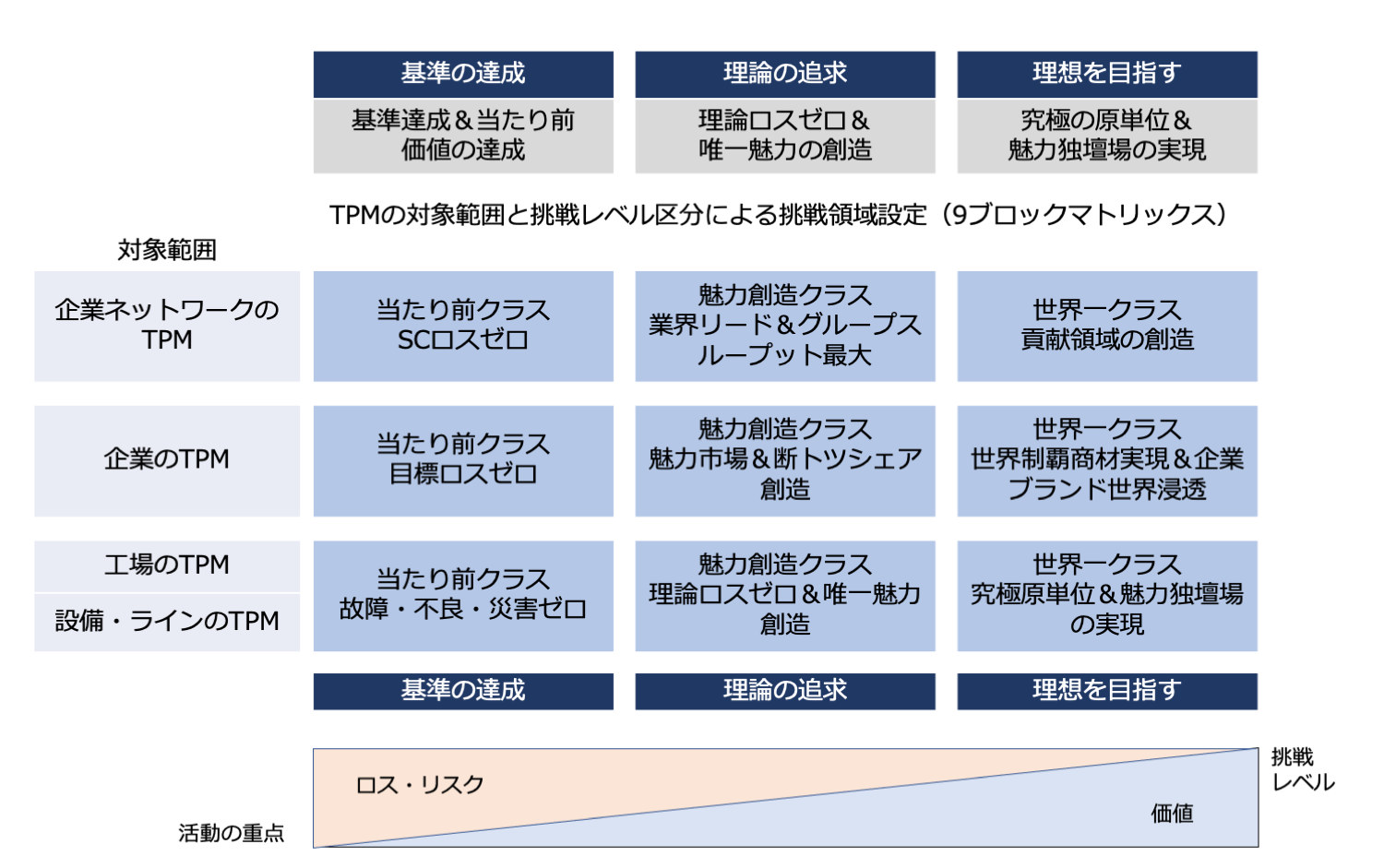
S-TPMの活動の道しるべは、基準・理論・理想に焦点を当てたものです(第2回参照)。この道しるべは「S-TPMの活動原理」とも言えます。この「S-TPMの活動原理」をベースに、ありとあらゆる手段を駆使してインプットの削減を継続していくことです。
a.レベル1追求の考え方
インプットの削減も「S-TPMの活動原理」をうまく活用します。
レベル1の当たり前の「○○基準レベル」をどんな環境でも常に達成しているか? 例外はないか? 例外が発生しているとすれば、どのような対策でそれを除去できるか? などを徹底的に研究していくべきです。これらを徹底していくと、例外や阻害要因による逸脱がなくなります。
さらに、「○○基準レベル」を突破した生産時間帯があったとき、そのときの環境条件や製造条件を調べます。うまくいったときの環境条件や製造条件をさらに突き詰めていくと、「過去最高記録」の生産性を達成できます。そこでこれまでの「○○基準レベル」を修正し、新しいより良い状態での「△△基準レベル」に再設定します。
次のレベル2で、現状の方法を理論的限界値まで攻めます。
b.レベル2追求の考え方
たとえば、現在の加工方法や製造方法・製造設備で材料歩留まり・設備総合効率の理論的な限界を追求することです。厳密な理論式を立てることができない場合でも、仮の計算で限界を見極めて、理論的な究極の効率を求めて攻めていくべきです。
事例:ボール盤の穴開け加工の例です。現行の設備総合効率(OEE)が30%。ドリルの切削時間とドリルを抜いて次の穴開け位置に移動するまでの時間はそれぞれ約50%短縮できます。しかし、現行の設備と材料のハンドリング方法では、材料と材料の間を可能な限り詰め、さらに穴開け個所の距離を短縮して移動時間を速めても、移動時間対加工時間の比率はほぼ1:4が理論的に限界です(シミュレーション計算)。その理論的限界値を目指して、ハンドリングや材料移動の時間短縮を工夫しました。ただ、この事例では現状の方法でOEEを85%以上にするのはムリがあります。マシニングセンターなどの材料の移動を自動化しないと、限界値以上のOEE向上は不可能であるということです。
次のレベル3で、現在の加工方法にとらわれないで「理想を目指す」ことになります
c.レベル3追求の考え方
理想レベルを追求するには、現状の方法・工法・現製品にとらわれることなく、自由な発想による革新が必要です。現行方法で極限値を追求していると理論的な限界が見えてきて、現行方法(現設備)を実施している限り、どうしても超えられない「生まれの悪さ」を実感することがあります。そこで現在の方法にとらわれることなく、どのような製造方法であれば最高の効率を実現できるのかを考えてください。
材料の歩留まり、理論サイクルタイムなど、現設備ではどうしても超えることができない制約でも、新しいつくり方を考えるとやすやすとクリアできることも多いのです。まだ同じ生産が継続し投資採算が取れそうであれば、躊躇することなく新しい生産方法を試行し、切り替えていく勇気を持つべきです。打ち抜き方式から、モールディング方式に変えたらコストが7分の1になった事例もあります。
従来のTPMで価値稼動時間(お金を生みだす時間)はロスとして捉えていなかった時間帯ですが、理論サイクルタイムの見直しや工法や方法を変えると、そのたびにさらに新しいロスが出てきます。インプットの削減についても従来のやり方に甘んじず、S-TPMでさらに究極のロス削減に挑戦していただきたいものです。
③設備生産性n倍化
①「ロス削減から価値付加向上へ」で述べた価値稼動時間の見直しについて、もう少し詳しく説明しておきます。
従来のTPMでは価値稼動時間はお金を産み出している時間なので、ある意味「ノータッチ」に近かったわけです。しかし、ここを攻めるのがS-TPMです。攻め方次第で設備生産性をn倍に増大する可能性があります(図8)。こんなにオイシイ話があるのに、そこへの挑戦は盲点になっていたせいか、これまで技術的な体系化がされてこなかったのです。この盲点ついて従来の改善成果のマンネリ化を打破したいものです。
図8 設備生産性n倍化への挑戦
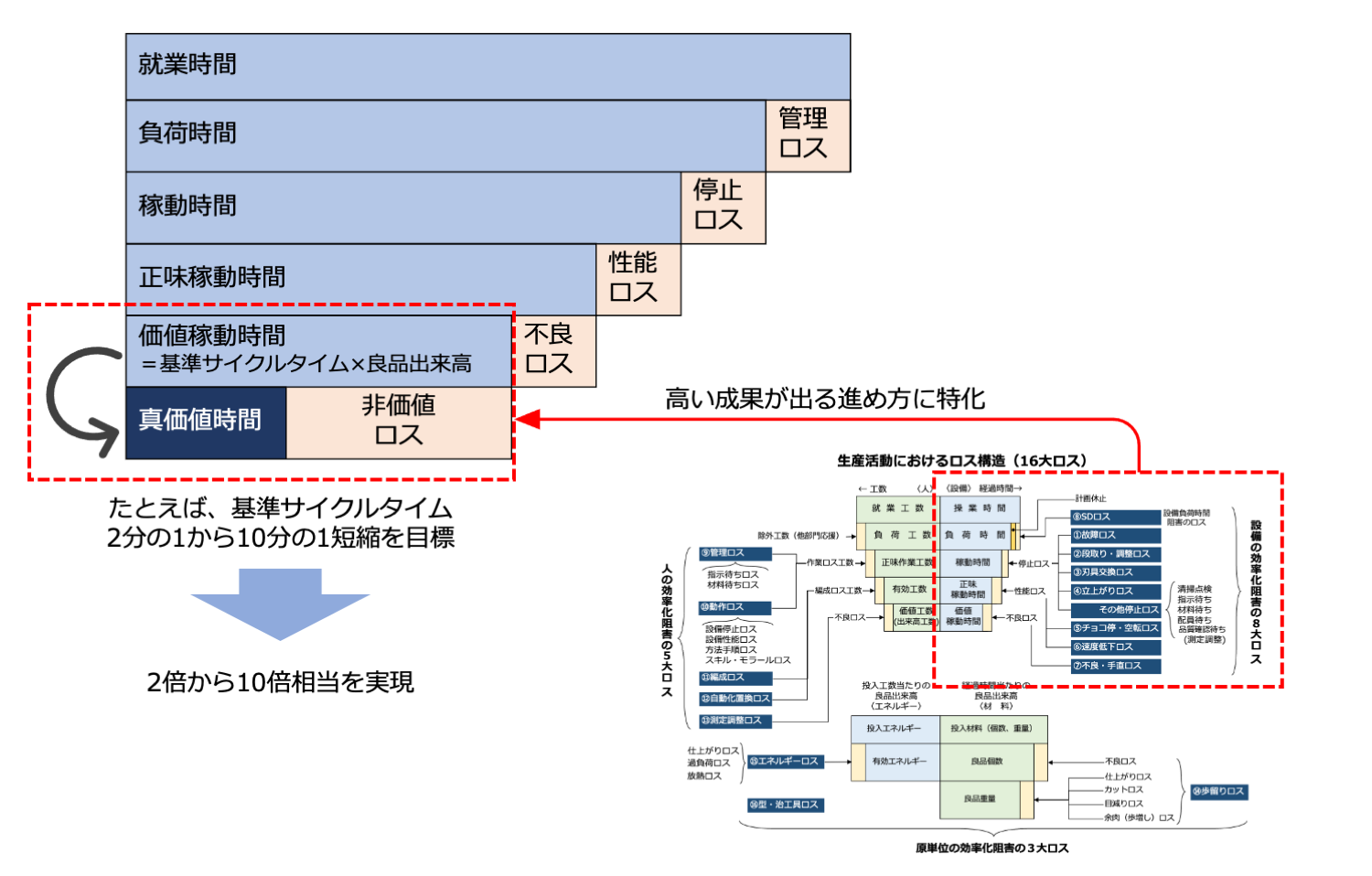
要点はこうです。従来の基準サイクルタイムを2分1~10分の1にすれば、設備生産性は2倍~10倍になるという論拠です。さらに製造で究極の付加価値が形成される瞬間は最終製品の形状が形成されるその一瞬であり、他はすべてロスと考えます。たとえば、切削の最後のひと削り以外はロス、組立の最後の締結固着以外はロス、塗装の表面乾燥固着以外はロス、と考えるのです。その実現手段は割愛しますが、従来の製造方法を延長して可能なこともあるし、少し設備やラインを改造して実現するやり方もあります。
筆者が支援してきたクライアントでは、工場の生産量を2倍にする要請があり、ミキサーがネック設備でした。そこでミキシング方法を改善することで4倍の能力にする支援を行いました。これで現行8台のミキサーを改造後は4台に減らして、16台分の能力にして、従来の2倍の生産量を達成することができました。このようなことは多数の企業で実現できているので、みなさんの企業や業種でも十分可能です。今後、価値稼動時間を大胆に攻めて、設備生産性n倍化に挑戦してみてください。
④工数半減アプローチ
すべての人の作業時間を半減することをねらった改善を「工数半減アプローチ」と呼びます。これは直接作業も間接作業(オフィス業務)も対象にしています。このアプローチを愚直に実施すれば、大幅な労務費などの削減が実現できます。人は本来もっと付加価値の高い業務に移行していくべきですが、現行の作業・業務構造が良くないために生産性が高くない仕事に従事しなければならないことも多く見受けられます。
工数半減アプローチで働き方改革を実現していくべきです。以下に、工数半減の観点と動作経済の原則を以下に整理しておきます。
【工数半減の観点】
1.距離半減:物理的空間的距離を半減以下に
2.同時動作:左右・次作業との同時化
3.待ちレス:空き時間をなくす
4.工程レス:工程機能の必要性を見極めてやめる
5.スピードアップ:制約を排除し、最速で動かす
【動作経済の原則】
足→腰→腕→指→目(限界まで時間短縮できる動きへ)
⑤すべての管理対象に管理指標を持つ
設備総合効率:OEEは、今やISOにも登録される(ISO22400参照)グローバルな設備効率化の指標となっています。それ以外にも、図2で<設備>以外にも<人><エネルギー><材料>のロスを示しましたが、それらに関わる指標をOHE:人総合効率、OE'E:エネルギー総合効率、OME:マテリアル総合効率など、管理すべき対象ごとに測定できる指標を設定することが大切です。「測定なくして管理なし」です。
OEEは、これまでに稼動率中心でカウントされていた設備の有効性に、目標の工程時間どおりに生産ができていないロスを顕在化することに貢献しました。同様に良品率も従来は製品不良の材料損失面でしか捉えられていなかった面を「不良品をつくってしまった時間もロスである」ことの重大性を気づかせてくれました。基本的なロスの定義の基盤は変えず、個々のロスは対象設備や企業ごとに独自に決めてロスの大きいところを重点にカウントしてもよいのです。このように考え方で進めれば、たいへん使い勝手の良い指標となるはずです。使い勝手が良くなれば、すべての対象に指標を設定してください。人・もの・エネルギーなど個々に管理指標を設けた効率化の物差し、個別改善の強化ツールそのものです。
⑥付加価値を創出できる個別改善
価値付加を創出する個別改善について詳しく述べます。
従来のTPMでは、提供する製品の付加価値を高めるための活動は対象外であることが多かったのです。しかし、厳しい経営環境の中、単純なロス改善だけでは大きな財務成果は出ませんし、ましてや顧客に選ばれる存在であり続けるのもの難しいのです。
そこで従来の事業やビジネスの延長線で実現できる付加価値向上を創出する個別改善を提唱したいと思います。
図9の上部に示すように、従来商材の価値の向上はインプットを削減してアウトプットを増やすことで実現できます。
図9 従来商材の付加価値を上げるには(レベルI)
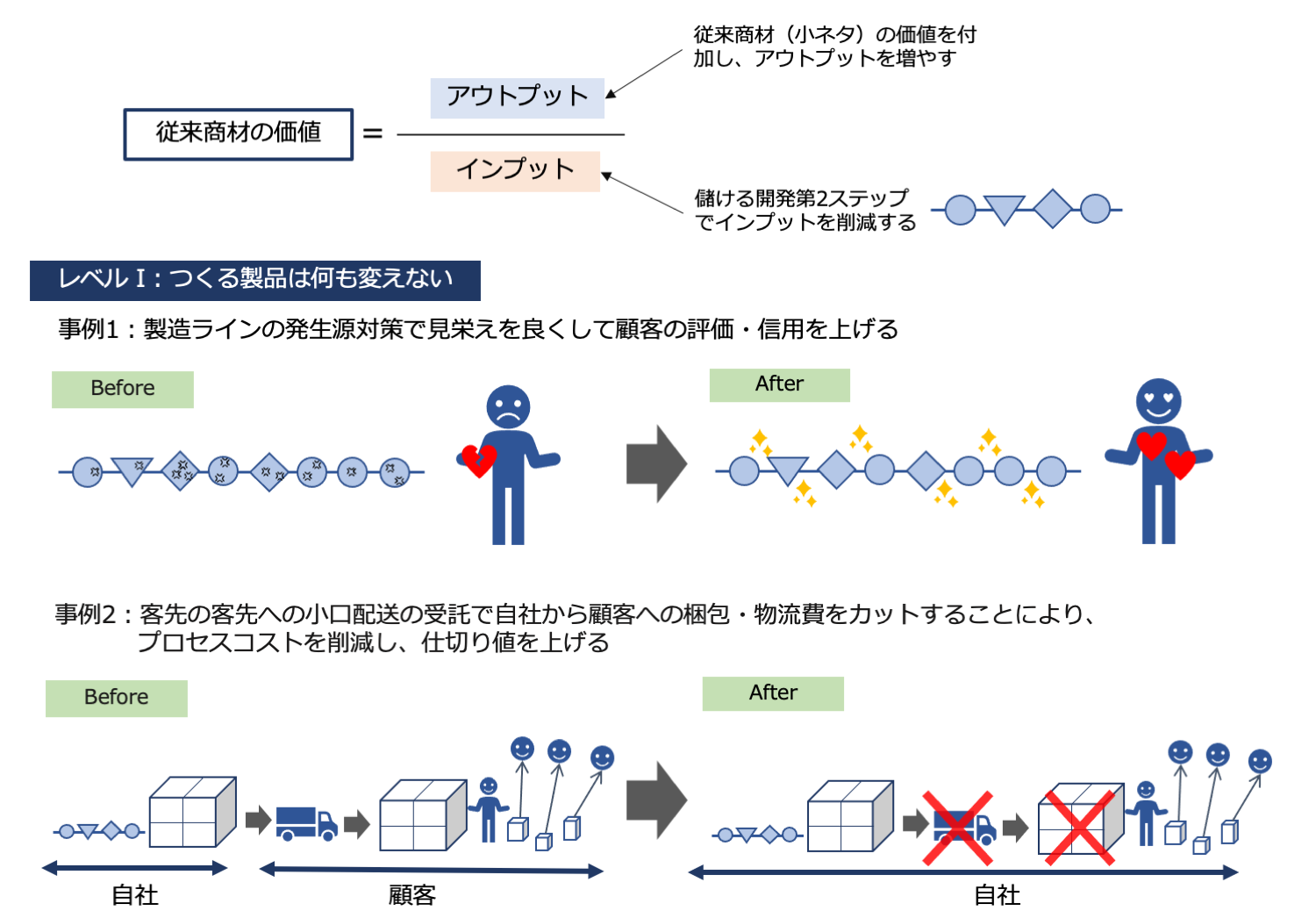
以下で活動範囲をレベルI~Ⅳの4つに分けて説明します。
レベル I:つくる製品は何も変えない
図9に示したレベルIはつくる製品はまったく何も変えないで自社の付加価値が上がるやり方です。事例1は製造ラインの発生源対策でとてもきれいな製造ラインを実現して、「こんな素晴らしい製造ラインで、それを実現・維持している人たちが製造していれば製品も安心である」という評価・信用を得る作戦である。
事例2では、製造・顧客提供プロセスのムダな部分を排除してインプットを抑え、相対的に粗利を向上させるやり方です。製品そのものは何も変更せず、相対的に付加価値を上げる作戦です。
従来、工場だけでは商材の付加価値向上に対しては何もできないと思われていたかもしれません。しかし、製造プロセスを改善したり、顧客のプロセスを取り込んだりすることで、その製造ラインで生産できるようにすれば、工場主体で付加価値を上げた製品を提供できたことになります。もちろん、営業部門に協力が必要ですが、十分に活動できるはずです。
レベル II:最終顧客への製品は変えない
レベル IIは最終の製品は変えないが、顧客の出費を抑える付加価値を自工程に取り込むことをねらいます(図10)。
図10 従来商材の付加価値を上げるには(レベルII)
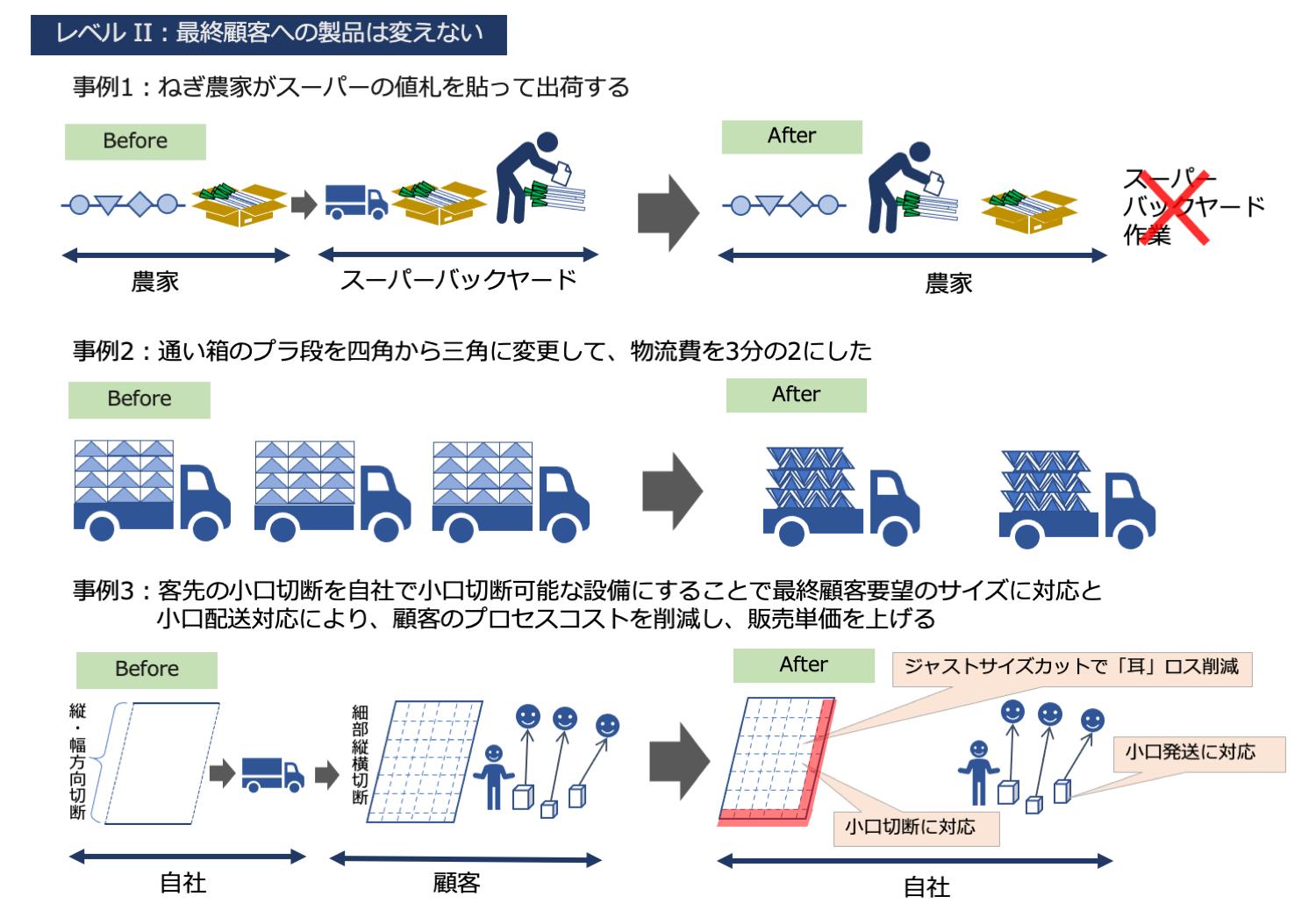
たとえば、事例1でねぎ農家がスーパーの値札貼りとトレーのパッキングを作業すれば、スーパーのバックヤード作業は不要になります。
事例2は、積載荷物の積載率を向上して運送台数を減らして物流費を下げた例です。
事例3は、自社で個別サイズの切断と小口配送を手掛けるようにした事例です。以前は、顧客が最終顧客の要望に従って個別サイズに切断して小口配送していました。そこで事前にサイズ情報などを顧客から入手して、個別サイズの切断と小口配送を行いました。自社から顧客への梱包・運送費も不要で、顧客の顧客である配送先をつかむこともできました。顧客から値下げ要求や転注がなくなり、自社の売上も大幅に向上しました
レベル Ⅲ:つくる商品も周囲も自由に変更
レベル Ⅲは、つくる製品やその周辺部材も自由に設計することをねらいます(図11)。
図11 従来商材の付加価値を上げるには(レベルⅢ)
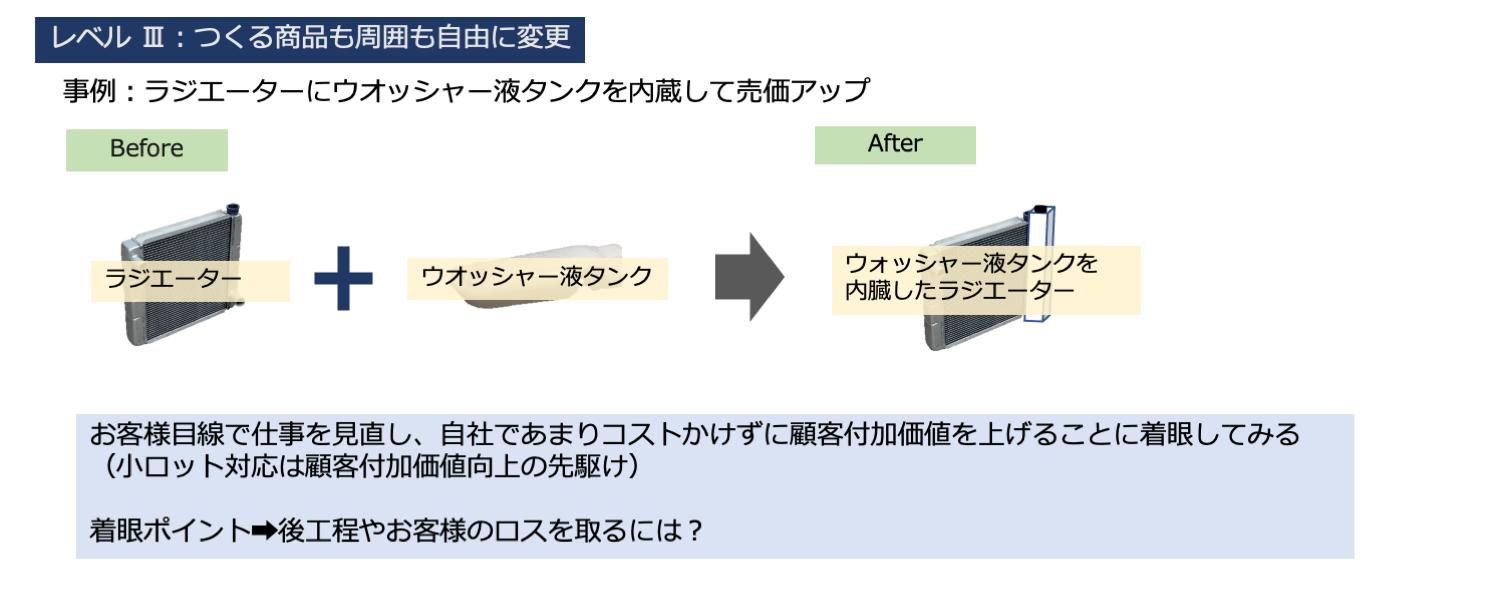
これはある程度の信頼と自社の責任体制を得てから顧客に提案していくイメージです。単品のコストダウンでは品質も落とせない状況では限界感、閉塞感があり、打ち手の限られたものになります。そこで、周りの周辺部材の費用も取り込んでトータルで考えることで大きな自由度が生まれ、新たなコストダウン策を生み出すことができるとする事例です。もちろん、前提として顧客がそれを受け入れてくれる必要があります。
レベルⅣ:顧客要望から吹っ切れてジャストミートする製品領域へ
レベルⅣは、目先の顧客要望から考えず、奥にある顧客の潜在ニーズを読み取り、従来にない顧客付加価値を洞察して提供することをねらいます(図12)。他社との差別化にたいへん有効な方法となります。もちろん、そのためには従来のアウトプットを超えるアウトプットを考える必要があります。
図12 従来商材の付加価値を上げるには(レベルⅣ)
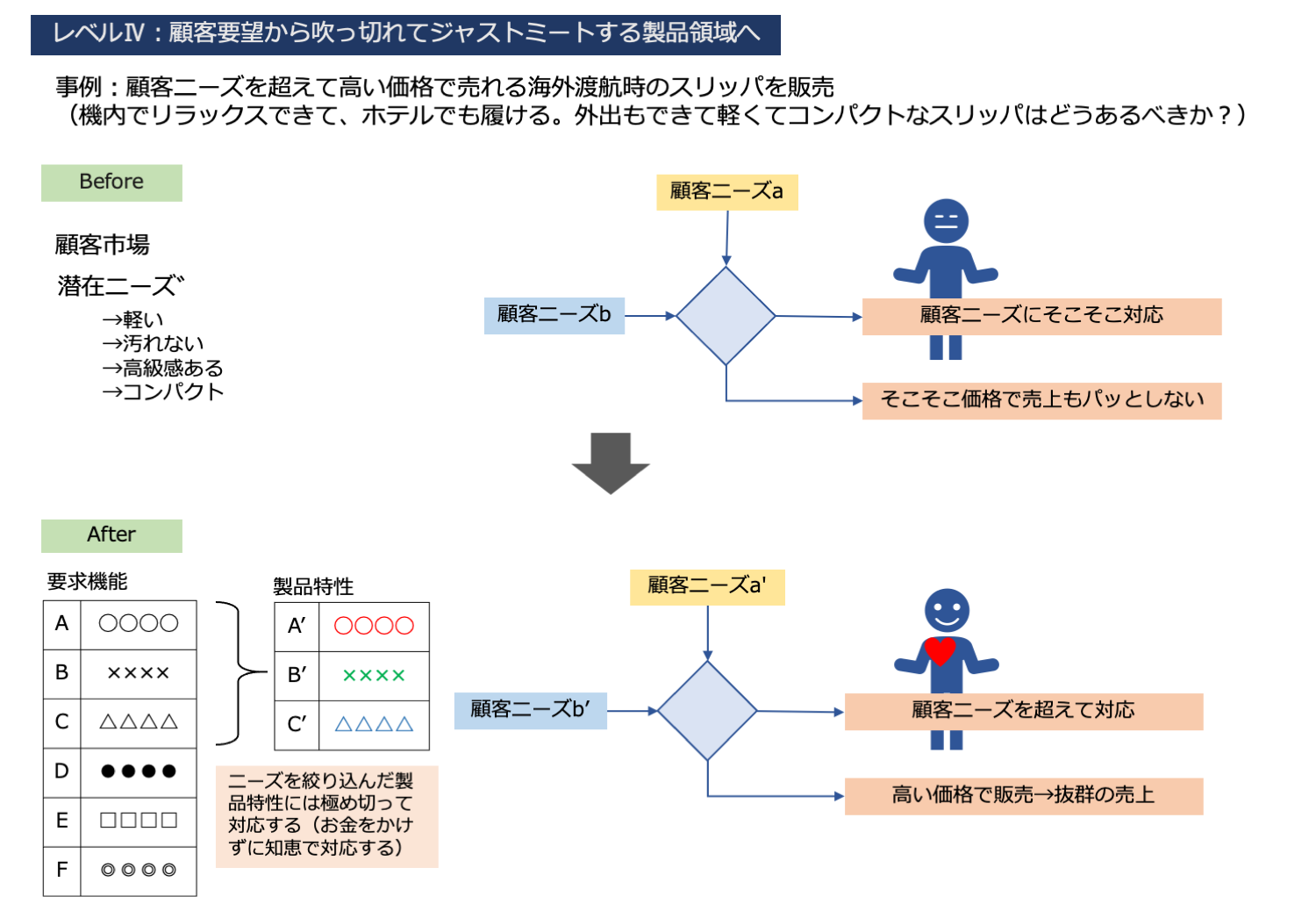
ところで、付加価値には一体どのようなものがあるでしょうか。下記に種類をまとめてみました。
【付加価値の種類】
・新機能
・新商品
・形状の大幅革新
・魅力価値(デザインなど)の増大
・その他(愛着・親しみ…etc.)
これらを従来のモデルチェンジで対応していたレベルで考えないでください。これまでにないレベル(格段に変革されたレベル)で、追加された価値ことが付加価値と言えます。このことを意識した活動で、従来を超える経営成果を出していただくことを期待しています。
従来の個別改善は、設備や人および原単位の削減を主とする効率化で、極言を恐れずに言うとインプットをいかに減らして同じものを生産するかという戦いでした。しかし、分母のインプットを減らすだけが、効率化手段ではありません。S-TPMでは分子を増やすこと(アウトプットの増大)、つまり付加価値向上の手段を深く考えることがもっとも重要であることがおわかりいただけたと思います。
■個別改善のレベル別のねらい
個別改善の進化レベルに合わせた、レベル別のねらいを図13に一例としてまとめてみました。自社の弱点を強化したり、目指すものを設定したりしてレベルを選択して、自社にマッチした個別改善を展開してください。詳細は別に機会に譲りますが、レベル別の付加価値獲得も含めて設定することで、大きな進展が見えてきます。
図13 個別改善のレベル別にねらうもの
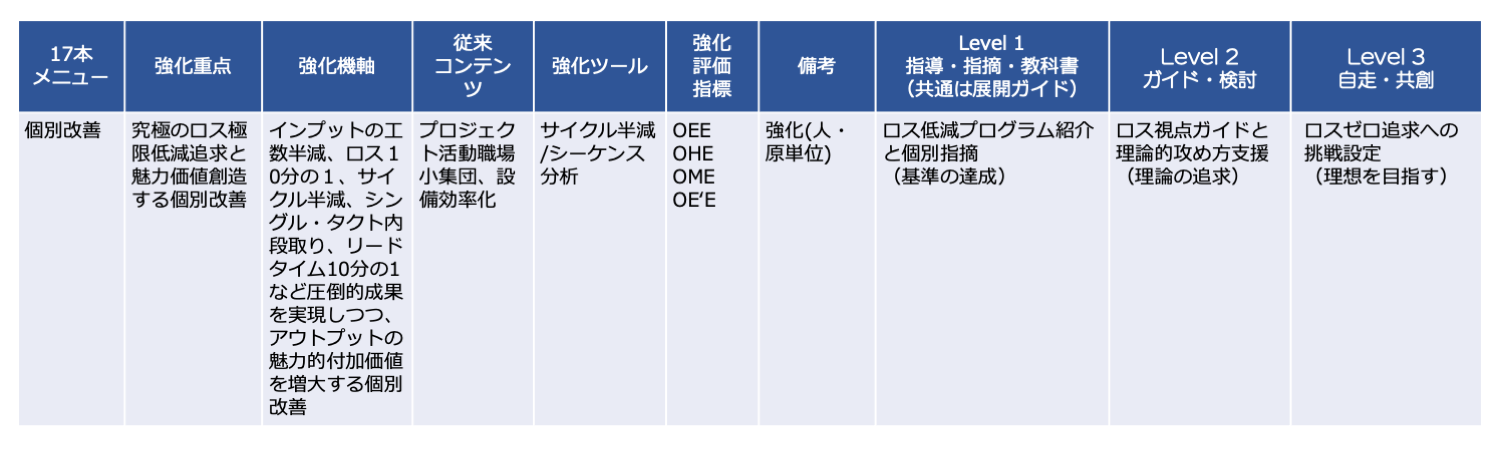
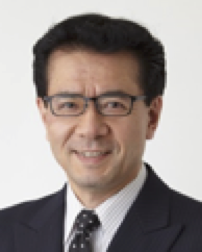
TPM革新センター シニア・コンサルタント
白濱 伸也(しらはま しんや)
1984年 JMAC入社。経営・生産・設備・間接領域におけるコンサルティング活動に従事。主要テーマは、経営戦略視点からのTPM展開支援、ビジネスプロセス革新、大幅コストダウン、リーンシックスシグマ展開支援、戦略的ISO9000&14000システム構築支援、生産システム設計、ヘルスケアコンサルティング、ビジネスモデル革新など。近年は、「17本のメニューに基づく新TPM(S-TPM)の推進者として提唱・普及に務めている。共著に『TPM成功の秘訣21』(JMAC)、『工場改善ハンドブック』(JMA)、『TPM展開ガイド』(JMAC)、『病院まるまる改善』(日本医療企画)、著作に『業務改革』(日本医療企画)、『儲ける開発』(JMAC)ほか多数、雑誌への寄稿も多数。
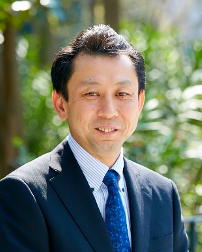
TPM革新センター チーフ・コンサルタント
場家 孝(ばっけ たかし)
2012年 JIPMソリューションに入社。TPMコンサルタントとして、さまざまな製造業を支援。前職は、住宅総合資材メーカーと医薬品製造業に勤め、TPM推進事務局をはじめ、製造現場、生産管理、物流、品質管理、品質保証、開発などの管理監督職を経験し、現職に至る。企業時代の経験を活して、各社にTPM活動支援を実施。支援は、国内をはじめタイ、インドネシア、トルコ、ブラジルなどの工場がある。
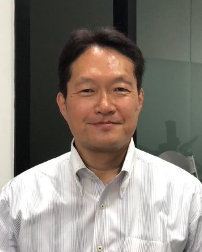
TPMコンサルティング事業本部
シニア・コンサルティングプランナー
石川 和秀(いしかわ かずひで)
1991年 日本プラントメンテナンス協会入職、JIPMソリューション経て現職。現在は国内外でTPM活動を柱とした新規顧客の開拓、また製薬企業を対象とした「医薬品業界における設備管理とGMPフォーラム」の企画運営を13年にわたり担当。「攻めて守る営業」「開発する営業」を中心に活動している。