「戦略的TPM」で新しいものづくり革新を―経営戦略とリンクする総合一貫型のTPMとは― No.12
第12回 S-TPMメニュー解説編 計画保全 S-TPMによる強化
計画保全 有機的な体制づくりで効果を出す
生産活動を効率的に行うためには、設備が一定の信頼度をもとに稼働することが基本です。そのための保全活動は計画的に実施するものと突発的な故障に対応する非計画的なものに分けられます。計画保全が有効に働けば、突発故障対応の事後保全の減少に繋がります。また、近年現場には正社員が減少してきており保全の機能強化は急務となっています。
計画保全の目的は、設備の設計・製作から運転・保全に至るまで、すなわち設備のライフサイクル全体にわたって、設備自体のコスト(IC)や保全などの維持費(RC)と設備の劣化による損失とのトータルコストを引き下げることにより企業の生産性や価値を高めることです。
計画保全体制を確立するには、設備の信頼性を高める活動を通じたアウトプットの向上(故障・不良)と、保全担当者の育成や組織の体質改善により関連する諸活動が効率的に実施されるための管理活動とを有機的に結合したシステムをつくり上げる必要があります。
とくにJMACの計画保全活動の特徴は、小集団活動で進めることです。推進していくには、人づくりや体質改善が不可欠です。その前提があってはじめて実効力ある保全戦略が可能となります。計画保全を通じて、人のマインドを変え設備を変え会社を変えていくのです。
■計画保全展開の10本柱
計画保全を展開するための10本柱を図1に示します。「1 計画保全の7ステップ活動」をマスタープランとして、他の9本の柱とリンクし連携を取りながら、計画保全を推進していきます。
図1 計画保全展開の10本柱(計画保全の実践)
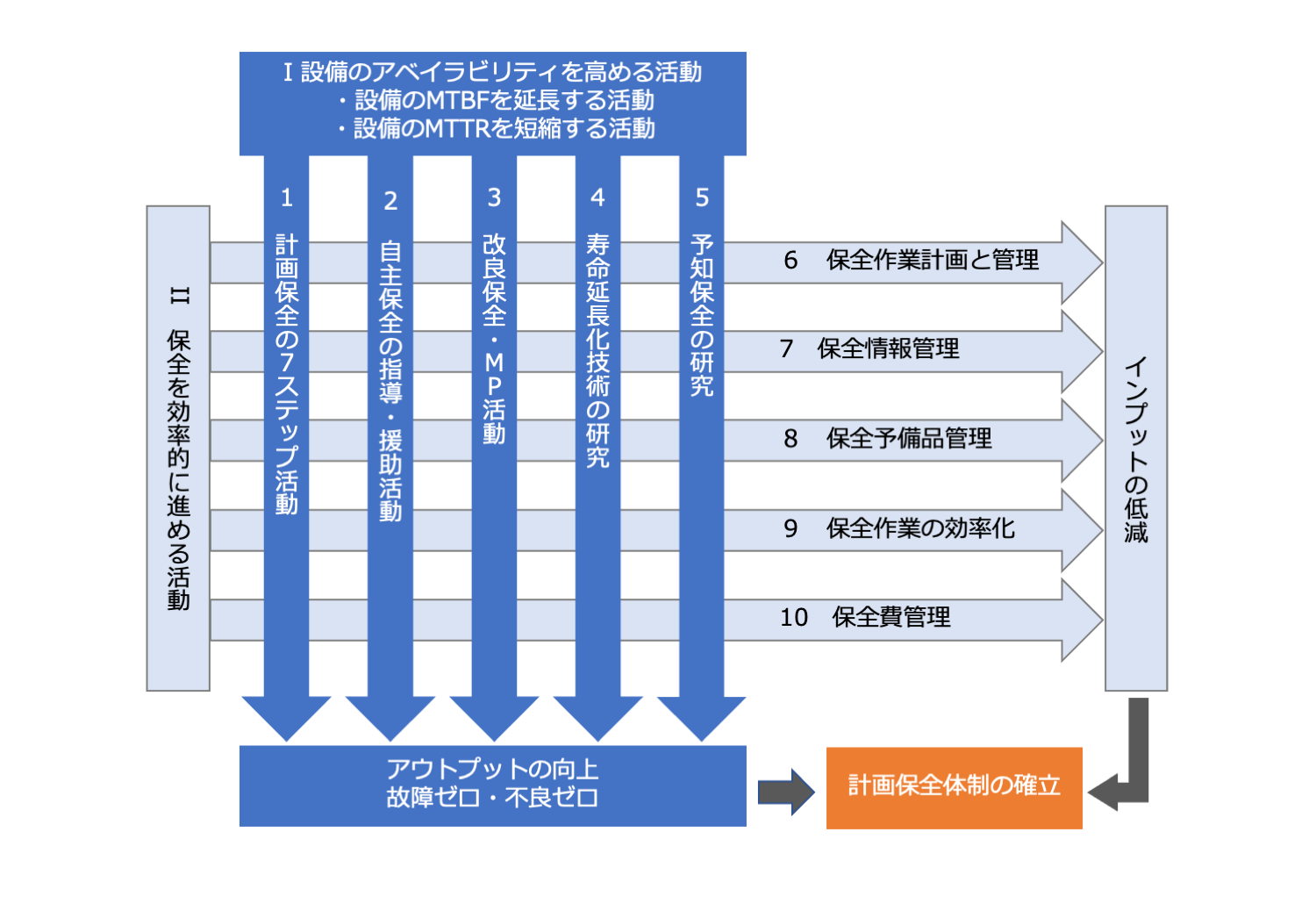
■計画保全の7ステップ活動
計画保全の7ステップには、設備をモデルにした活動と重点部品をモデルにした活動があります。
設備をモデルとした活動は、設備単位に故障を減らすことを目的としています。一方、重点部品モデルはどの設備にも共通的に使用されている部品を中心として、部品単位で故障を減らすことを目的としています。
これらの活動と自主保全との関連を整理したのが図2です。活動をうまくリンクさせて推進することで、設備の信頼性を確保します。
図2 計画保全の7ステップ活動
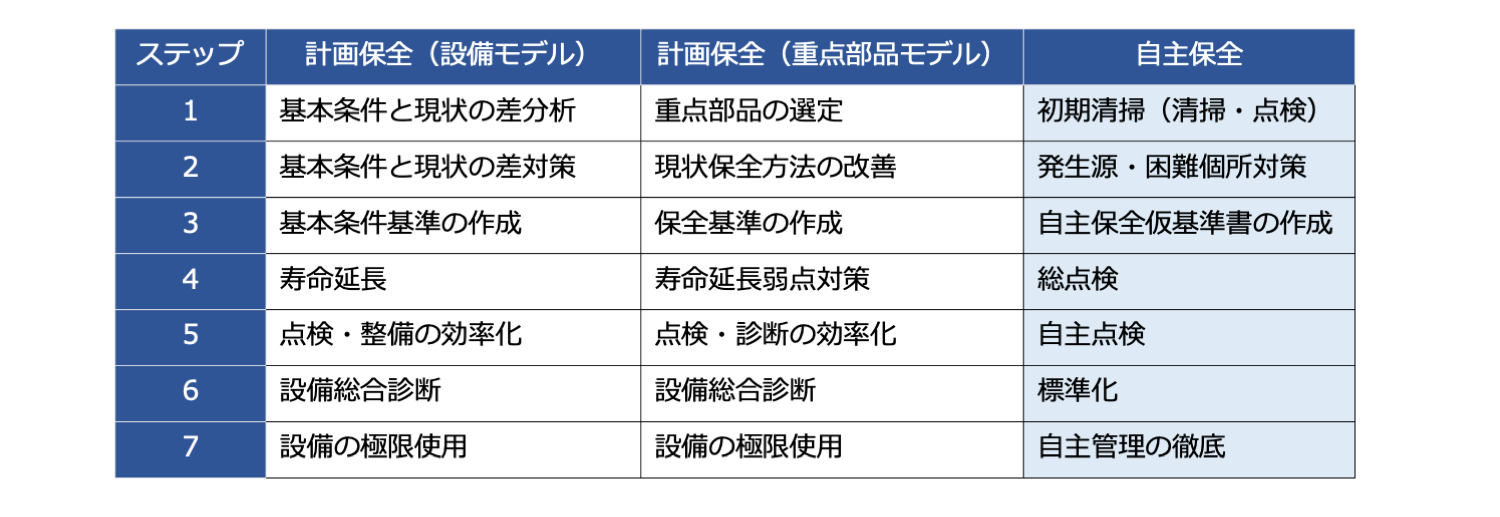
■計画保全体制構築のポイントと事例
計画保全体制づくりでは情報システムの構築も必要となるため、進め方の例として手順とねらいを図3にまとめました。さらに、具体的なポイントを説明していきます。
図3 設備保全システムの構築ステップ
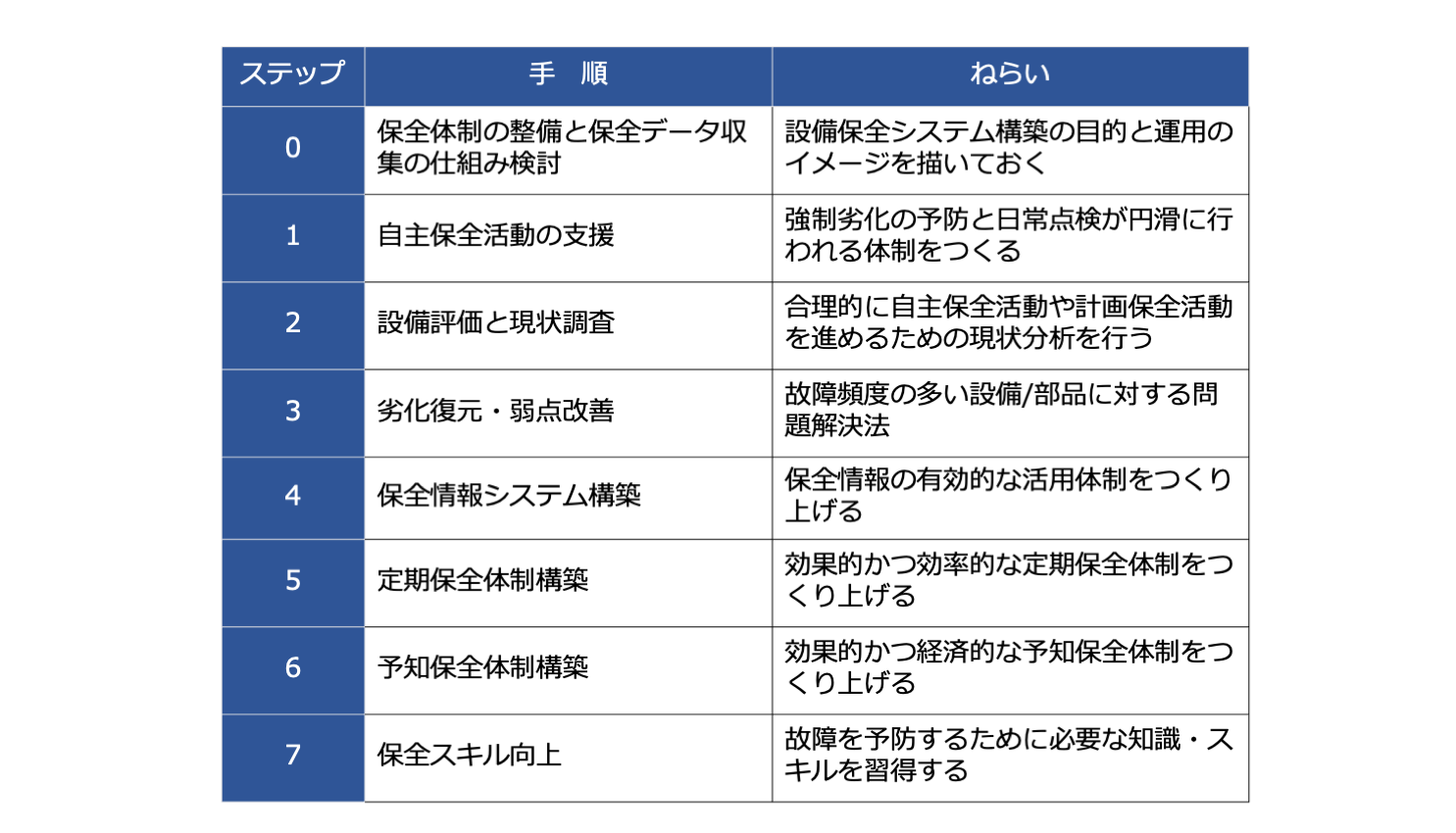
ステップ 0:保全体制の整備と保全データ収集の仕組み検討
ねらいは「設備保全システム構築により何を達成するのか? 成果を得るために活動進捗をどうモニタリングするか?」を明確にすることです。
活動内容は、①設備リストのアップデート、②点検/保全/修繕に用いる頂上の整備・自主保全支援担当の明確化、③計画保全活動の明確化--となります。
ポイントは、設備保全システム構築手順と各ステップのねらいと目標の理解することです。
ステップ1:自主保全活動の支援
ねらいは、強制劣化の防止や軽微レベルでの不具合の発見と迅速な処置ができる体制づくりです。
活動内容は、①基本条件や使用条件の教育、②不具合発見のための知識・スキル教育、③不具合処置対応、④総点検教育支援、⑤OPL(ワンポイント・レッスン)の標準化--です。
ポイントは、①不具合の優先順位づけの検討、②保全から見て正しいOPLとなっているかのチェックです。
ステップ2:設備の評価と現状調査
ねらいは、合理的に自主保全活動や計画保全活動を進めるための現状分析を行うことです。
内容としては、①設備の重要度ランキング、②予防保全対策対象設備の明確化、③予防保全対象設備の現状の信頼性評価--となります。
ポイントは、①設備の重要度ランキングとして「安全」「品質」「停止時間」の順に検討、②故障の頻度またはMTBFを用いた信頼性評価です。すなわち、絶対に故障してはいけない設備(部位)を評価するということです。
ステップ3:劣化復元・弱点改善
2ステップでは評価と現状調査を実施して優先順位を決めました。このステップでのねらいは、故障発生頻度(寿命延長)の優先度の高い設備/部品に対し、問題解決法を適用することです。
図中にある劣化復元とは、自主保全活動の復元まで時間がかかる設備や自主保全活動そのものができない設備(オペレーターが1人しかいない設備やユーティリティ)については保全部門が対応するということです。
弱点改善とは寿命が短い設備・部品の寿命を延ばしていく段階です。
ステップ4:保全情報システム構築
ねらいは、設備保全情報の有効活用による「設備故障の予防」「納得のいく予備品管理」「納得のいく保全予算管理体制」の実現です。
活動内容は、①設備保全情報方式の検討、②整備検査計画とその記録の考察、③帳票/データ出力法とその活用法の検討--です。
ポイントは、①保全単位の検討(予備品管理に関連する)、②保全単位ごとの作業方法・技能の明確化、③故障記録とその活用法の検討--です。
保全情報システム構築とは、単にPC上で稼動する「情報ツール」の導入することではありません。
ここでの保全情報システムとは、設備・ユニット・組立部品・部品の構成において、部品レベルでどのような保全でどのような周期で実施するかを決めて、さらに作業を標準化して、全設備に対して基準化していくことを意味しています。
設備・ユニット・部品までを財務として見れば、資産管理・予備品管理につながります。また、保全の周期は保全予算管理・外注管理に、OPLや標準は技能評価につながります。OPLを作成しても、それを守れる人がいなければ、いずれ故障が発生します。守れるように教育が必要です。このように単に情報ツールを入れるだけではなく、人や仕組みとの関わりに着目して、全体を一気通貫で見ることができるようにしていくのが保全情報システム構築のねらいです。
図4 設備情報の出力と活用(保全情報システム構築)
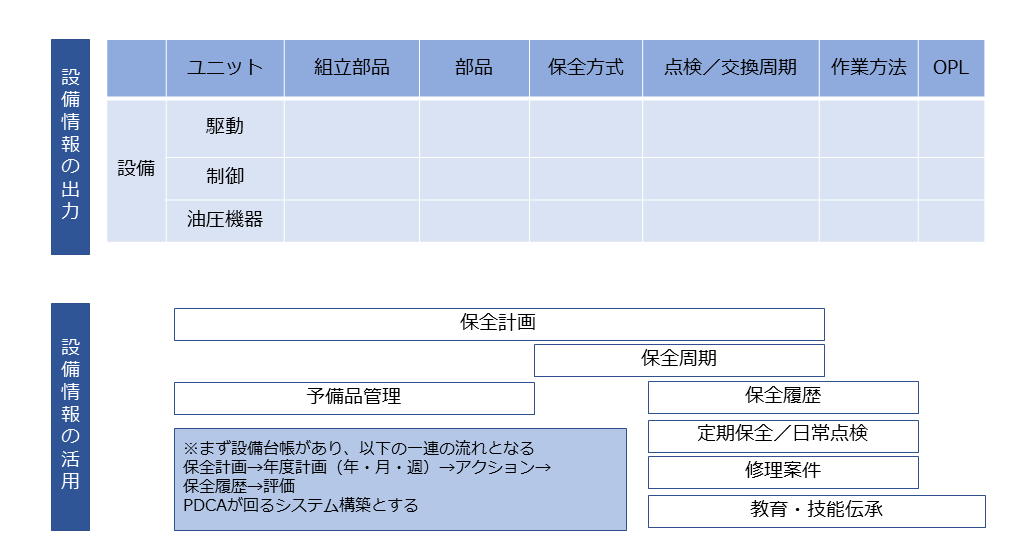
※JMACでは、情報システム構築のツールとしてPLANTIAを推奨しています。PLANTIAはIoTシステムを使用し保全業務フローを回すだけで、保全計画とその実施内容の情報が自動的に収集されるデータベースにします。PLANTIAにフィッティング、連携させることで簡易的なデータ収集ができる仕組みを提供します。
ステップ5:定期保全体制構築
ねらいは、定期保全の実施により、「設備故障の予防」「効率的な定期保全への見直し」を実現することです。
その内容は、①定期保全フローの作成、②保全単位ごとの保全周期の確認とカレンダー作成です。
ポイントは、定期保全前に故障が起きた場合、故障解析し周期や方法を見直すことです。逆に交換後に劣化速度が遅いと判断した場合には、周期を見直す必要があります。
ステップ6:予知保全体制構築
ねらいは、予知保全の運用により、部品の極限使用をしながら設備故障を予防し、経済的な取替による保全経費の最適な利用を目指すことです。
内容は、①予知保全が合理的であると考えられる対象(部位)の検討、②部位ごとの劣パターンと劣化検出技術の検討、③劣化パターンのイメージ作成と異常値が検出された場合の処置の明確化--です。
設備ごとに物理パラメータが異なるため、適切な物理量(振動、電力、変位など)を見極めながらセンシングの技術を上げていく必要があります。
ステップ7:保全スキル向上
ねらいは、保全担当者の知識・スキルを向上させ、設備故障を予防し故障が発生しても安全で短時間で修復できるようになることです。
その内容は、①保全単位ごとの作業スキル評価と弱点面の教育、②要素技術教育です。
ポイントは、作業単位ごとに作業性を評価することで保全標準の実効性を高めることです。また、保全困難個所の改善テーマにも取り組みます。
以上のステップ4~7はとくに密接した活動であることを強調しておきます。保全システムを構築することで、対象とする設備に必要な保全方式、交換周期、傾向管理(電流診断など)の必要性の有無が見えてきます。また、技能としては定期交換のスキル、電流診断計による電流波形の解析スキルをどう育成すればよいかが見えてきます。すなわち、決められた周期ごとに取れ替える定期保全、電流診断の実施・活用による予知保全、それらを支える人を育成する保全スキルの向上が同時に進むことになります。
冒頭に述べたように計画保全を確立するには、設備の信頼性を高める活動を通じて、アウトプットの向上(故障・不良減)と保全担当者の体質改善を有機的に結合していくことと言えます。
S-TPMで計画保全を強化
■計画保全の近年の困りごととその対策方向
前半でベーシックな計画保全を解説しました。基本を確認していただいたところで、計画保全の近年の困りごととその対策方向、およびS-TPMとしての強化事例を紹介していきます。
近年の計画保全では、本来の保全の強化に貢献してきた計画保全体制づくりや故障削減にあまり効果が出てないなど、基本的な側面(これをやればこの効果が出るはず)での成果が出にくくなっているようです。もちろんその背景には、設備の高度化が進み、複雑で解析が困難な故障現象も増えていることもあるでしょう。しかし、設備が故障して本来の機能が発揮できない時間が増えているということは、設備を知って使いこなしていく「保全の力が相対的に落ちている」と言わざるを得ません。
図5に近年の計画保全の困りごとと対策方向を示します。このほかにも困りごとはあるでしょうが、対応方向は類似していると思われるのでこの図を参考にしてみてください。
図5 近年の計画保全の困りごとと対策方向
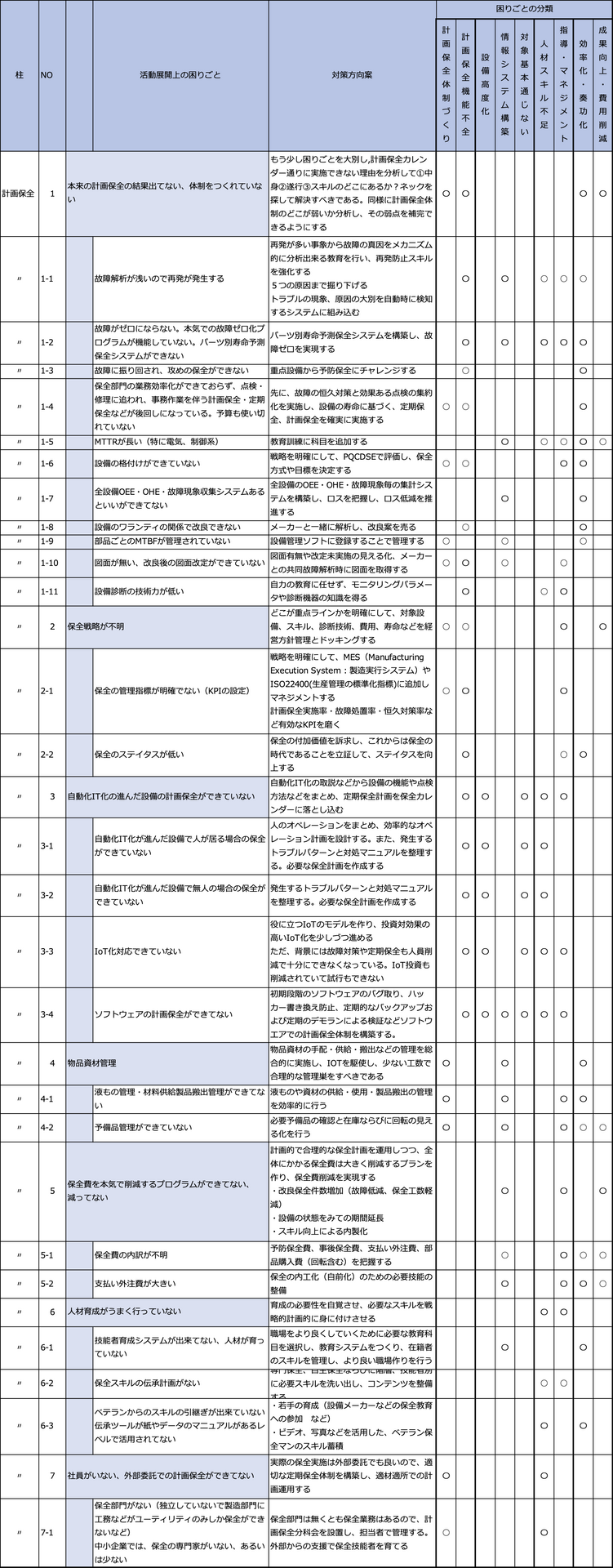
これらの困りごとと対策方向をグルーピングしてみると、
①計画保全体制とその機能不全
②設備高度化などへの応用力不足
③人材育成やマネジメント力不足
④経営成果向上力不足
の4つに大別できます。
総じて言えることは、基礎がしっかりできてきないせいか環境や対象が変化すると問題解決できなくなる、問題解決力が低下する、ということです。これらの弱点も踏まえて、S-TPMとしての計画保全の強化事例を紹介します。
■S-TPMとしての計画保全の強化事例
強化された計画保全とは、「製造設備総資産(リソース)のこの上ない合理的な保全を体系化する計画保全」です。前節で述べたように、高度化する設備やソフトウェアに囲まれ、複雑でかつ省人化された「悩み多き職場」になっている現状があります。この状況を打破には、戦うべき対象を明確にして過去のナレッジを十分活用し、この上ない合理的な計画保全体制を構築して成果を上げなければなりません。そのために役に立つ強化ポイントを以下に整理しました。
①パーツ別寿命予測による故障ゼロシステム
多くの保全方式を採用しつつも、まだ故障ゼロに至っていない、あるいは最近の保全部門の力量低下で故障が増えているのであれば、パーツ別寿命予測による故障がゼロ化のアプローチを推奨します。これが遠回りのようで近道です。簡単にその概要を説明します。
最初は台帳づくりです。設備の格づけにあまりとらわれず、故障の多いエリアをモデルにして、できるだけそのエリアの設備をパーツ別に分解した台帳にしておきます。次に台帳にあるパーツ別の寿命予測です。そのパーツの寿命が来る前に交換すればいいわけです。寿命予測が当たっていれば、この理屈で故障ゼロが実現できるはずです。
これで故障ゼロにならなかった場合は、パーツの寿命予測が間違っていたか、パーツ周りの使用環境が安定せず強制劣化が進み、予定より早く壊れたことになります。したがって、強制劣化の原因を探して改善すれば、その場所の故障ゼロが実現できていきます。もちろん、パーツ別の寿命予測で寿命が短すぎて部品交換が頻発して停止の頻度も多くなることもあります。そのときはパーツの使用環境を改善したり、もっと寿命の長いタイプのパーツに変更したりして、保全周期を延ばす必要があります。また、発生した故障に関しても故障解析で真因を除去することで、その故障現象を根絶すべきです。
実際、このやり方で故障ゼロを達成した企業が増えています。
②全設備OEE・OHE・故障現象収集による稼動管理システム
現在IoT化が進んでいるとはいえ、旧型の設備や単体マシンではまだ全設備の稼動率を自動的に収集できるレベルにはなっていません。そのため、日報に記載したデータや生産実績データを組み合わせて集計しているのが実情です。
今後はこれらの設備も含めて、全設備の稼動率、性能稼動率、良品率を設備から直接収集する仕組みをつくるべきです。人による収集の手間やエラーがなくなります。
対象設備をどう捉えるか、データ収集の全体の仕組みをどう考えるかが大事です。図6は個々の設備と接続してデータを集めている例で、高稼動な稼動管理システムを実現しています。また、これは人の稼働にも応用できます。
図6 設備総合効率データの収集例
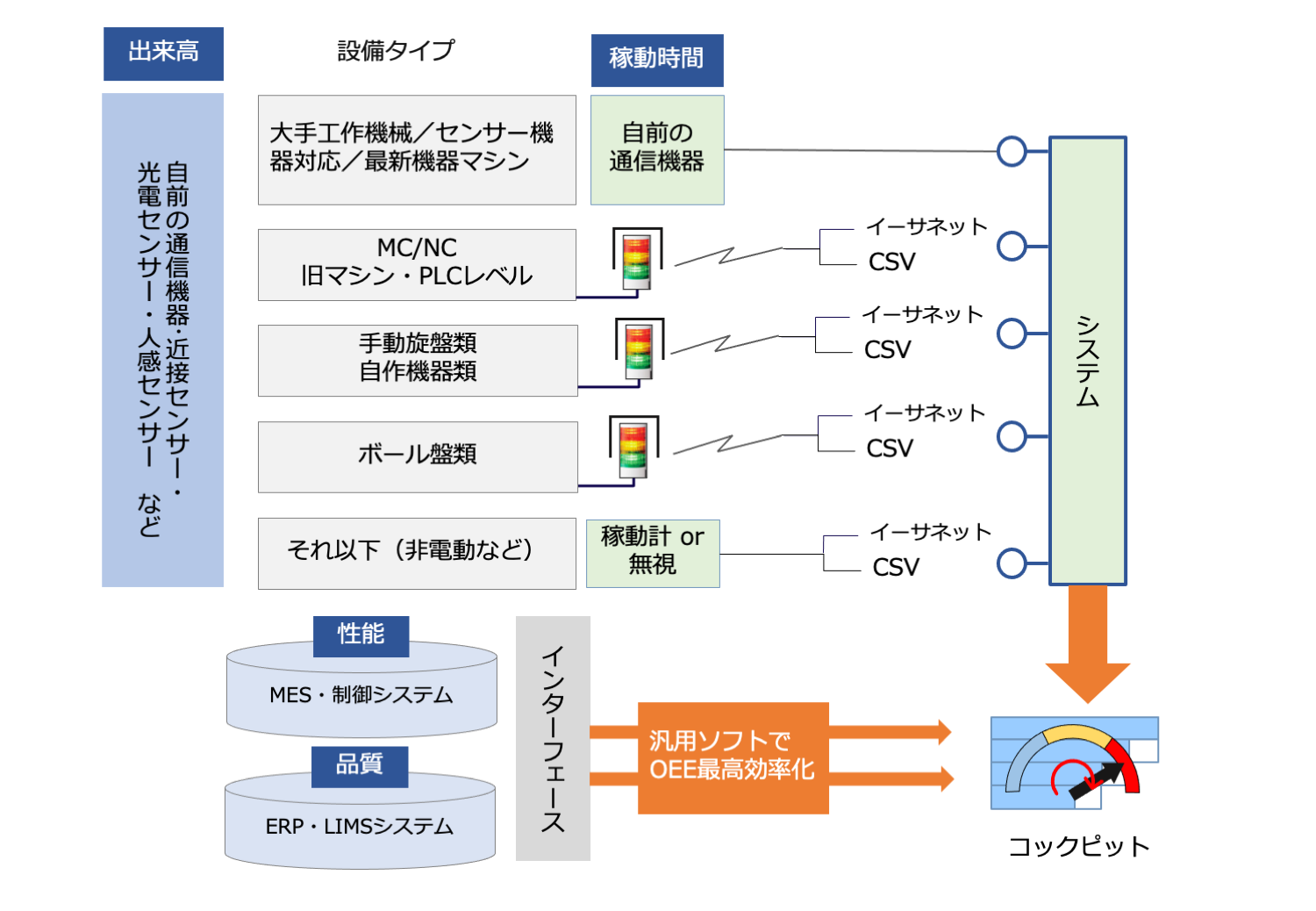
③製造材料や設備使用部材・液ものなど全供給搬出管理システム
設備に製品材料や部品および副資材などすべての供給と排出を総合的に管理する仕組みを最初から考えることでトータルに掛かる点検や供給搬出に掛かる人手を極小化できる。
図7は「液もの」の使用・供給体系図の例です。IoT機器を活用することで「使用部」における「液もの」の枯渇状況や劣化状態を把握することが可能になり、供給部における「液もの」の「自動補充や資材発注システム」につなぐことができます。
図7 「液もの」の使用・供給体系図(例)
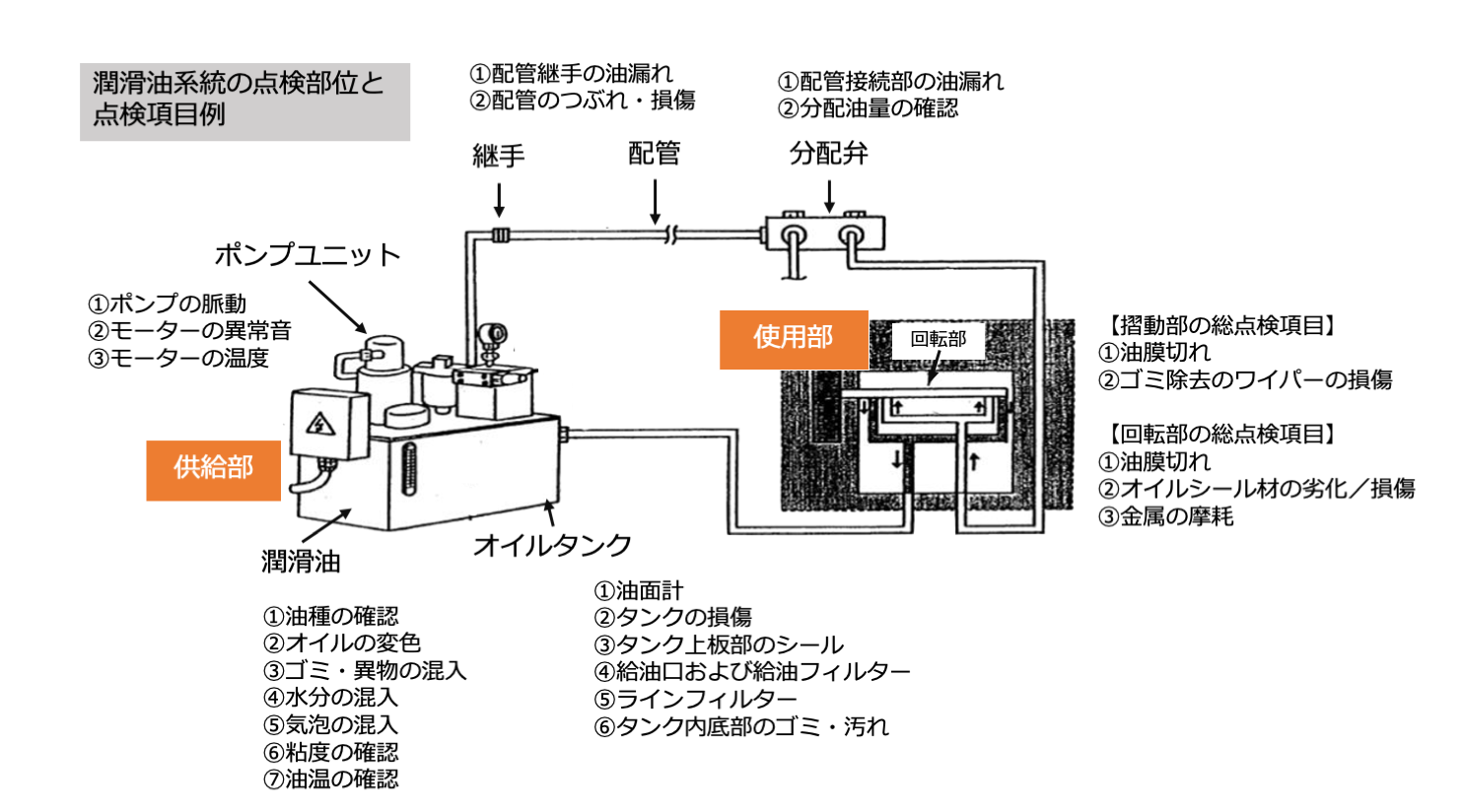
④クロスリアリティ(X Reality:VR・AR・MR・SRの総称)を活用した技能伝承システム
ベテランの保全技術者が少なくなる中、保全技術の伝承の必要性が叫ばれている。しかし、教える方と教わる方が接する時間は、従来と比べて大幅に減少しています。こうした中で将来有望視されているのが、XR技術を活用した教育訓練&技能伝承システムです。
図8に示すように、保全対象となる現物の設備をウェアラブル端末で見ると、目の前には実際の設備に重ね合わせて、作業手順、作業指示、禁止事項のガイドなどをバーチャルな画像で指示してくれます。配線図や設計図などの図面類を参照するも、騒音に強い骨伝導のマイクで指示すればスマートグラスの画面に必要な図面を表示できます。
また、作業中にわからない点や疑問点が出たら、現場の実態を撮影しながらベテランに質問します。該当作業にマッチした的確な指示を受けながら、知識不足を補いつつ、確信を持って正確な保全作業を実施することができます。もちろん、作業記録も撮影され、作業値や作業時間のログも記録できます。
図8 XR機器を使った技能伝承システム(例)
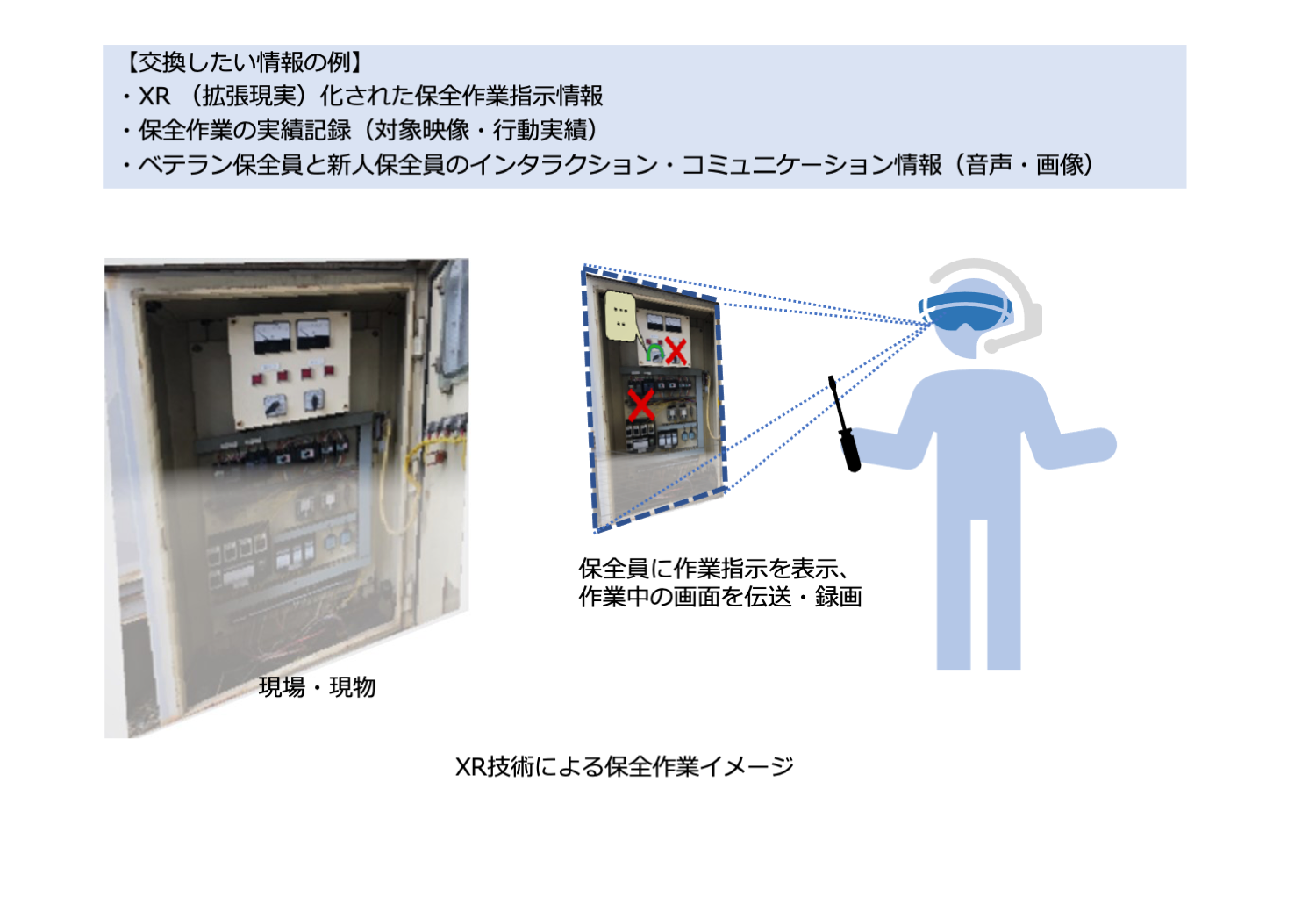
⑤保全費を本気で削減する仕組み
高度化した設備が増え、既存設備の老朽化が進み、自ら実施できない保全業務が増えて外注費が増加するなどで、保全費の削減がたいへん困難な時代になっています。しかし、ここで諦めてしまうと、保全費はますます増大するので注意が必要です。
まずは基本に忠実に、図9の右にあるように自社の保全費の内訳を詳細に調べます。新規設備はイニシャルコストだけでなく、点検や保全費も含めて費用を極小化し、設備保全費のコストダウンをコツコツと地道に計画的に進めていくことです。これは一見遠回りのようですが、一番着実なコストダウンになります。
図9 ライフサイクルコストにおける保全費の位置づけ
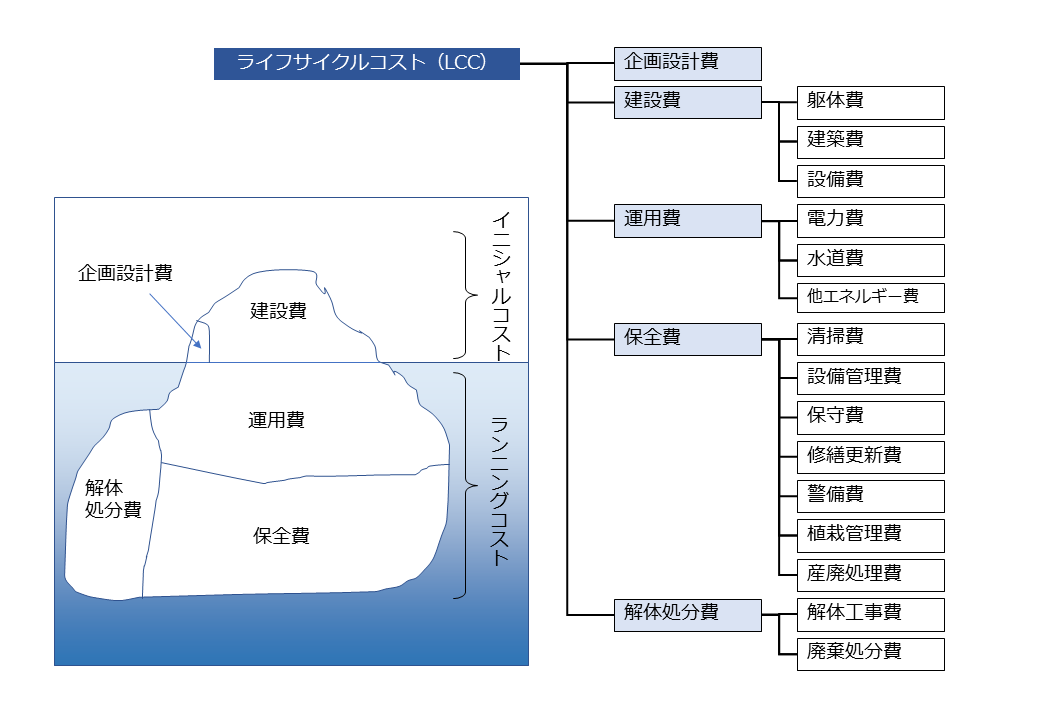
次は成り行きのコスト構造を正していきます。図9の左部にあるようにライフサイクルコストの2~3割がイニシャルコストの建設費です。ランニングコストは水面下に入っていて、一見目立たなくなっています。しかし、本気で保全費およびライフサイクルコストを削減するためには、最初から建設費だけでなく、保全費・運用費・解体処分費も最小なるようにすべきです。そのためには、たとえ企画設計費が増えたとしても全体の調査やシミュレーションおよび事前のつくり込みが重要です。
現在はデジタル化が進んできたので、各種の設備類の導入実績のデータをデータベースに登録して、企画設計の時点で最終的なライフサイクルコストがミニマムになる手段や仕様を採用していくべきです。ただ、ミスターTPMこと中嶋清一氏が「ライフサイクルコストのデータが集まりにくいので、各企業は苦労している」と指摘されたことがあります。その当時はなぜ難しいのかを理解できませんでしたが、「ある部品を選定しても使用の負荷率、保全の程度により、必ずしも一定のライフサイクルを全うできるわけではない」ということから、今になってその難しさがわかってきました。中嶋氏の指摘もこのことを意味していたのだと思います。
今後のデータとしては、部品の設計上の寿命や故障情報に加え、該当部品の使用条件(負荷率や平均的環境温度、および保全程度)も同時に保存しておき、それらを収集できるようにしておくことです。実際には、そのような細かい差の発生よりも、設計時に使用時のことを考えないために発生するランニングコストが増大することも認識しておいてください。まずは図9のように、運転時や保全時にも手が掛からず、運用費・保全費・解体処分費などのランニングコストを少なくする配慮が重要です。
「本気で減らす」ための保全費低減の進め方を以下に整理しました。
【本気で減らす保全費低減の進め方(例)】
1.企画設計時に保全作業や保全費および運用費を下げる企画・設計・製作し、運用を設計しつくしての設備導入実施
2.部品・材料の寿命延長
3.部品・材料の再生使用
4.定期整備周期の見直し
5.保全作業方法の見直し
・清掃・点検・補充・修理・分解整備・計画・記録など
6.保全工事の内外製見直し
7.予備品および管理の見直し
・事前設備ティアダウンで予備品安価化・標準化・在庫・保管方法・発注先および方法など
8.故障の低減
9.重点費目内訳の分解・見直し
10.エリア別・設備別・担当者別費用過多の部分の削減
11.運用費、修繕費、更新費など回りから下げる
12.水道光熱費やユーティリティ費、他の費用の低減
13.外部依頼(工事・整備・点検などすべて)の内製化
従来の保全費低減への着眼に加えて、設備の企画・設計・製作時点から保全費・運用費も含めたライフサイクルコスト全体を調べつくします。それで評価した設備、ユーティリティ設備、建屋を、工事・設置・運用していくようにします。また、設備のティアダウンによる安価予備品の開発も重要です。もし、完全に企画設計時点までさかのぼれない場合でも、できる範囲からそれぞれの着眼ポイントを実施してください。
このように具体的に示せれば、人間関係の調整やコミュニケーションに不慣れな新人や若手にも理解しやすく、有効な観点になると信じています。
■計画保全のレベル別のねらい
計画保全の進化に合わせた、レベル別のねらいを図10に一例としてまとめました。自社の現時点でのレベルに合わせて、レベル1、レベル2、レベル3と挑戦目標を設定し、自社にマッチした将来のものづくりを支える計画保全を展開してください。詳細は割愛しますが、これを機会に「この上なく合理的な製造設備総資産の保全」のためのプランニングを行うことを願っています。
図10 計画保全のレベル別にねらうもの
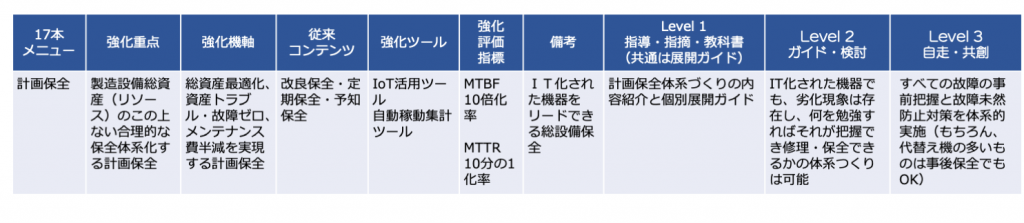
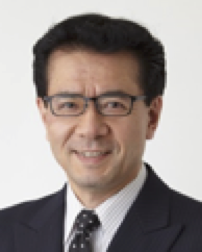
TPM革新センター シニア・コンサルタント
白濱 伸也(しらはま しんや)
1984年 JMAC入社。経営・生産・設備・間接領域におけるコンサルティング活動に従事。主要テーマは、経営戦略視点からのTPM展開支援、ビジネスプロセス革新、大幅コストダウン、リーンシックスシグマ展開支援、戦略的ISO9000&14000システム構築支援、生産システム設計、ヘルスケアコンサルティング、ビジネスモデル革新など。近年は、「17本のメニューに基づく新TPM(S-TPM)の推進者として提唱・普及に務めている。共著に『TPM成功の秘訣21』(JMAC)、『工場改善ハンドブック』(JMA)、『TPM展開ガイド』(JMAC)、『病院まるまる改善』(日本医療企画)、著作に『業務改革』(日本医療企画)、『儲ける開発』(JMAC)ほか多数、雑誌への寄稿も多数。
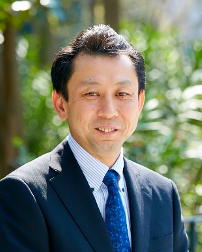
TPM革新センター チーフ・コンサルタント
場家 孝(ばっけ たかし)
2012年 JIPMソリューションに入社。TPMコンサルタントとして、さまざまな製造業を支援。前職は、住宅総合資材メーカーと医薬品製造業に勤め、TPM推進事務局をはじめ、製造現場、生産管理、物流、品質管理、品質保証、開発などの管理監督職を経験し、現職に至る。企業時代の経験を活して、各社にTPM活動支援を実施。支援は、国内をはじめタイ、インドネシア、トルコ、ブラジルなどの工場がある。
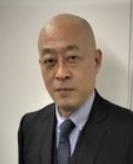
AutomotiveTPM推進センター センター長
プロフェッショナル・コンサルティングプランナー
石黒 透(いしぐろ とおる)
1996年 日本プラントメンテナンス協会入職、中部地区にて研究会運営や会員企業向けサービスを展開。JIPMソリューションを経てJMAC現職。中部地区、自動車産業、海外(主に中国)の各社にTPM活動、コンサルティング支援を実施。