「もうイヤッ!」のその前にTPM 連載第1回
みなさんが初めて配属された工場で、よく見かけたり、耳にしたりする3文字のアルファベット「TPM」。何の略語だろうかと不思議に思った人も多いかと思います。TPMは後でも詳しく述べるとおり「災害ゼロ」「不良ゼロ」「故障ゼロ」の3つのゼロを、全員参加で実現して生産効率を上げる活動です。しかし、実際に活動を始めてみると奥が深かったり、また時には誤解が生じたり、初心を忘れたりすることも多々あるようです。そこで今回から始まる「まんがで学ぶTPMの基礎」シリーズは、いま一度TPMの基礎の基礎に立ち戻って、その概要をやさしく解説します。
→左から右に読んでね
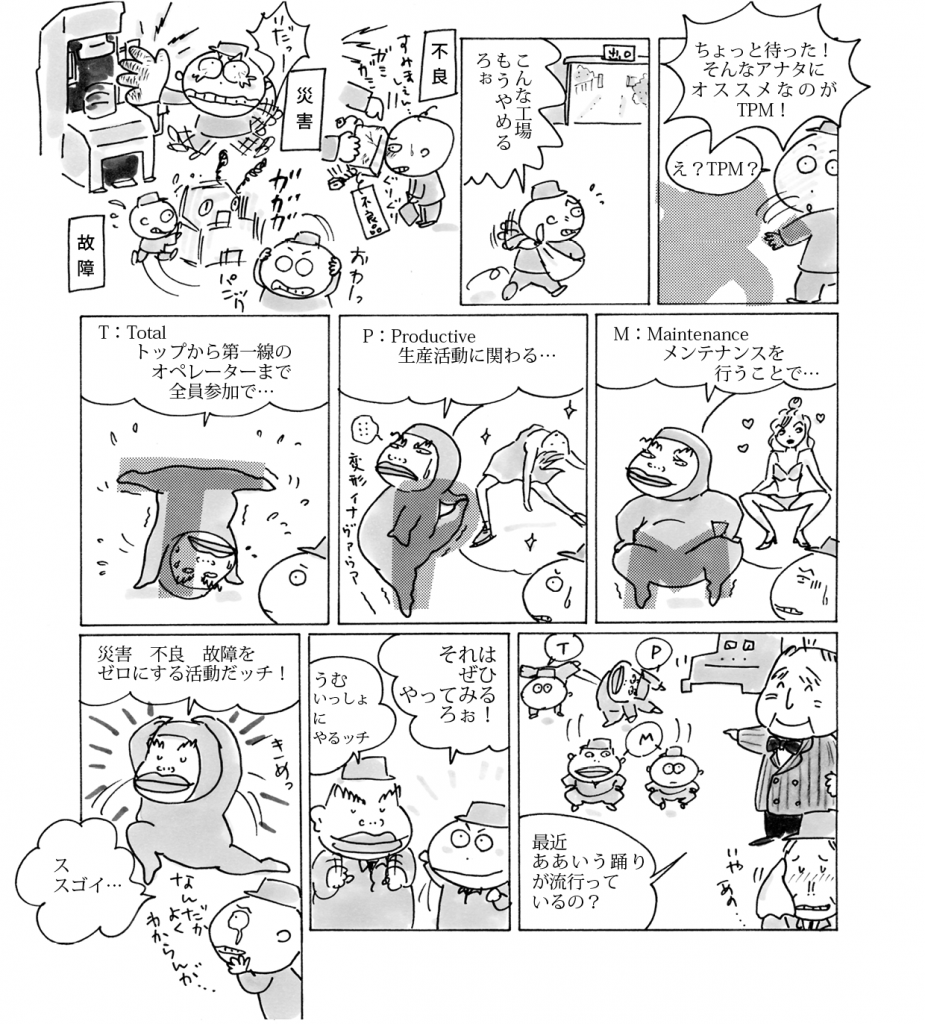
ここがポイント!
TPMって何?
TPMとはTotal Productive Maintenance(=全員参加の生産保全)の頭文字をとった略語です。簡単にいうと、「災害ゼロ」「不良ゼロ」「故障ゼロ」の3つのゼロを、全員参加で実現して生産効率を上げる活動ですが、詳しくは、
1.生産システム効率化の極限追求(総合的効率化)をする企業体質づくりを目標にして、
2.生産システムのライフサイクル全体を対象とした「災害ゼロ、不良ゼロ、故障ゼロ」など、あらゆるロスを未然防止する仕組みを現場・現物で構築し、
3.生産部門をはじめ、開発・営業・管理などのあらゆる部門にわたって、
4.トップから第一線従業員まで全員が参加し、
5.重複小集団活動によってロスゼロを達成する
活動と定義されています。
なぜTPMを導入するのか
「全員参加っていわれても、保全作業には保全部門のスタッフがいるじゃないか」。オペレーターなら誰しもそう思うことでしょう。
もちろん、従来は設備が正常に働いてくれるように保全をするのは保全部門の役割でした。しかし近年は、工場の生産設備はますます自動化・高速化されてきて、もはや「設備がモノをつくっている」といっても過言ではない状況です。そうした状況下では、保全部門だけの保全活動では無理が生じるようになってきました。どうしてもオペレーターや、設備や製品開発担当の部門など、すべての人の参加が不可欠なのです。
とくにオペレーターにとっては、故障や不良を出さないために、1人ひとりが「自分の設備は自分で守る」といった考えを持つことや「設備に強いオペレーターになる」ことが大切になってきます。
TPMのねらい
TPMは「人と設備の体質改善による企業の体質改善」をねらいとしています。
私たちの働く職場は、まさにロスの集合体です。では誰がそのロスを生み出しているのかというと、それはそこで働くトップから第一線のオペレーターまで、すべての人たちの行動によると言えます。その行動の源は、「これで当たり前」「自分たちのせいではない」という考え方ではないでしょうか。こうした考えがある限り、ロスをゼロにすることはできません。つまり、人の体質改善が必要なのです。
人が変わることにより、設備の体質改善が図られ、故障や不良をはじめとするロスがなくなります。このように、人と設備の体質改善を行うことによって、ロスをなくした「儲ける企業体質づくり」が実現するのです。
コラム:日本で生まれた世界のTPM
「設備は故障してから修理するもの」という考えが当たり前だった日本に、1951年、アメリカから「設備が故障する前に保全する」という予防保全の考え方が入ってきました。その後、設備を故障しにくく、保全や修理がしやすいように改善する「改良保全」や、設計段階から故障しにくく、保全しやすくしておく「保全予防」の考え方が生まれました。これらの考えが統合され確立されたのが「生産保全」(PM:Productive Maintenance)という手法です。そのPMに全員参加(Total)という日本的な発想を取り入れられました。それが、TPMです。そんな日本生まれのTPMも、現在では海外でもグローバルに展開中。いまや、世界のTPMとなっています。