【第10回】チョコ停改善の7ステップ展開③
3ステップ:微欠陥・不具合の摘出と復元・改善
微欠陥の摘出
(1) 微欠陥とは
チョコ停現象の分析やその発生メカニズムの解明が終わったら、微欠陥の提出と復元・改善を行う。
微欠陥とはこれ以上小さくできない欠陥のことで、キズ、クラック、欠け、摩耗、緩み、脱落、断線、汚れ、異物付着、異音、振動、異温などを指し、これらが単独または複合的に絡み合って、チョコ停などの現象を引き起こす(図)。チョコ停の多くは、微欠陥によって発生している。
微欠陥
(2) まずは基本条件の徹底を
微欠陥・不具合を摘出・復元するに当たって大前提となることは、現場の基本条件(清掃・給油・増締め)の整備を十分に行うことである。この基本条件が維持徹底されていないために、チョコ停が発生していると言っても過言ではない。
清掃しないと汚れが駆動部、摺胴部、検出・制御部に入り込み、摩耗の促進や感度の低下などになり、チョコ停につながる。たとえば、ワークとの接触面やパスライン(製品の通り道)の清掃を怠ると、汚れが堆積し、パスラインの汚れによる抵抗によってシュートが詰まり、チョコ停が発生するというメカニズムが考えられるためである。
ゆるみについても、ネジが1つゆるんでいれば他の締結部へストレスを与え、それも次第にゆるんでいく、
また、給油も適正な油種、給油の周期や方法などを守っていなければ、機械精度が悪化していくものである。
まずは、清掃点検をとおし、悪さを明確にすることが必要である。
(3) 微欠陥の発見
微欠陥を発見するにあたっては、外観形状的に微小なものを見つけ出すことが必要となる。そのためにルーペや簡易拡大鏡、マイクロスコープなどを用い、五感による観察の精度向上に努めたい。また、その他の測定器の活用や発見方法の研究も重要である。
微欠陥は放っておくと成長し、ガタがガタを呼ぶといわれるように他の部品へも劣化を誘発させ、全体のバランスが崩れることにつながるので、小さいうちに芽を摘むことが肝要である。
(4) あるべき姿との比較や理屈で考える
微欠陥を見つけるためには、感度を上げる必要があるが、あるべき姿(必要条件と十分条件を兼ね備えた状態)との比較や理屈で考えることも重要である。そうすることで、あやしいと思われるものをすべて摘出し、悪いものをすべて直し、その結果解決できるという場合がほとんどである(図)。
あるべき姿(V ベルト3 本がけの例)
微欠陥の排除と復元
微欠陥を見つけ出したら、しっかり復元を行う。チョコ停を起こしている設備はこれまでは使い放しの状態であり、各部位が劣化し最初の常態から変化しているはずである。まずは復元し設備を設置したときの状態に戻す。
また、設備の部品に至るまでの構造を理解することが必要となるため、機構図を作成し、個々の部品の劣化モードとチョコ停や他の不具合との関連を把握する。
機構図の作成(例)
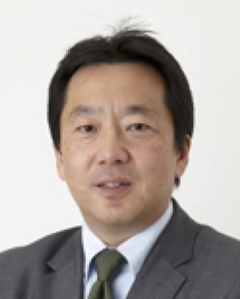
TPMコンサルティング事業本部 顧問
和泉 高雄(いずみ たかお)
1984年 日本能率協会(JMA)入職。日本プラントメンテナンス協会、JIPMソリューションを経て、2013年にJMAC取締役、19年から現職。国内外の工場・ものづくりの現場のコンサルティング、審査は100社以上。専門分野のPM分析、個別改善、自主保全、品質保全に加え、TPM全般の教育にも定評がある。共著に『TPM展開プログラム・加工組立編』『PM分析の進め方』(いずれもJIPM)、編著に『チョコ停改善はこうやれ!』(JMAC)、雑誌への寄稿および講演多数。全日本能率連盟認定マスター・マネジメント・コンサルタント(J-MCMC16007)、国際公認経営コンサルティング協会認定コンサルタント(CMC)、TPM Award審査委員。早稲田大学理工学術院非常勤講師。