【第8回】チョコ停改善の7ステップ展開①
チョコ停・空転ロスを撲滅するには、
① 現状把握
② 現状の分析
③ 微欠陥・不具合の摘出と復元
④ 結果の確認
⑤ 最適条件の検討
⑥ MTBFの延長
⑦ 無人化への挑戦
という7つのステップを踏んで展開する必要がある(下図)。
チョコ停ロス改善の7ステップ
こうした手順をふまえないと、要因が把握できなかったり、チョコ停が再発するなど改善の効果が得られないこととなる。
以下にチョコ停・空転ロス改善の7ステップ展開を紹介する。
ステップ1:現状把握 チョコ停ロスの明確化(マクロ的把握)
(1) ロスのマクロ的把握
チョコ停ロスは、その大きさに気づかないところに大きな問題がある。チョコ停をゼロにするには、まずロスとしてはっきりと認識することが重要である。
ロスを明確に捉えるためには、ロスをマクロ的につかむことと、ミクロ的に把握することの両方の方法がある。
マクロ的とは、設備の稼動時間の中でチョコ停が影響し、生産量やコスト目標に対し未達か否かの判断を行うことである。まずは、マクロ的にチョコ停を把握することになる。
(2) ネック工程を把握
マクロ的把握の手順として初めに行うべきことは、加工強度時間を測定し、ネック工程を把握することである。加工強度時間=基準CT/設備総合効率で求める(負荷時間に対し、良品1個つくるのに要する時間を計算)。
ここでのポイントは、各工程の能力バランスを確認することである。ネック工程の設備がチョコ停時間の占有率が高いのであれば、詳細なチョコ停マップやチェックシートを用い、チョコ停ネックの見える化を行うとよい。
チョコ停マップの例
(3) チョコ停の見える化
つぎにチョコ停のゼロを目指し、活動板を用い、全体のチョコ停の見える化を行う。
つまり、ライン全体、設備別の発生件数を月および日々のデータを把握し、改善のスピードと対策後の確認をできるようにする。処置や原因対策をした後、どのくらいで再び発生するか。とくに清掃や微欠陥を排除してもどの周期で変化が起きるのかを確認し、基準書に反映したり、寿命延長の対策につなげる。
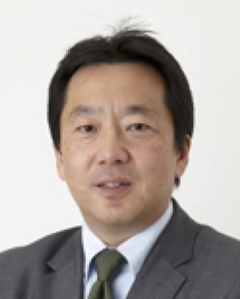
TPMコンサルティング事業本部 顧問
和泉 高雄(いずみ たかお)
1984年 日本能率協会(JMA)入職。日本プラントメンテナンス協会、JIPMソリューションを経て、2013年にJMAC取締役、19年から現職。国内外の工場・ものづくりの現場のコンサルティング、審査は100社以上。専門分野のPM分析、個別改善、自主保全、品質保全に加え、TPM全般の教育にも定評がある。共著に『TPM展開プログラム・加工組立編』『PM分析の進め方』(いずれもJIPM)、編著に『チョコ停改善はこうやれ!』(JMAC)、雑誌への寄稿および講演多数。全日本能率連盟認定マスター・マネジメント・コンサルタント(J-MCMC16007)、国際公認経営コンサルティング協会認定コンサルタント(CMC)、TPM Award審査委員。早稲田大学理工学術院非常勤講師。