竹内 康二 Koji TAKEUCHI
竹内 康二 (たけうち こうじ)
日本能率協会コンサルティング
プロフェッショナルアドバイザー
TPMコンサルタント
チャレンジしてみよう! 人は成功体験で成長する
◆改善は失敗を恐れず、最後までやり続ける勇気を持とう!
どのような時代になっても、生産現場では故障や不良などのロスや将来に向けた課題に対して前向きに取り組むことが必要です。このためにはまず、これらのロスや困りごとを正しく認識し、その原因を突き止め、改善行動ができる知識と技能を有する人材が不可欠です。しかし、このような人材は企業内でも少ない上に、解決すべき問題や課題は更に増えています。
この解決のための強力な武器となるのが、現場での実践的な人材育成プログラムであるTPM活動です。現場で身近な設備に触れ、不具合を発見して修復することで改善を学び、この改善効果を体験することで改善成果と自己成長に喜びを感じ、次の改善へチャレンジができるのです。
改善ができる人材の育成は、簡単で小さな問題から取り組み、小さな成功体験を経験させることが重要です。失敗を恐れず、成功するまでチャレンジしましょう。
◆現場に密着した改善活動から方針管理による会社経営まで豊富な経験が大きな力に
出身企業では、はじめに製造現場の技術員としてアルミ筐体部品を主体に、加工工場の品質管理と品質改善業務に携わりました。その後、加工設備導入からNCプログラム作成、QC工程図、作業標準作成と作業者教育までの生産準備業務から生産立上げの一連業務を経験して、設備知識と加工知識を活用し工場全体の不良削減と、品質クレーム対策や生産性向上に取り組みました。
あわせて、国際取引のパスポートであるI SO9001やQS9000の取得に向けた品質システム構築と、製造現場での品質管理体制の整備と強化を経験したことで、ロスの未然防止の思想においては個別改善以上に、自主保全活動の自主点検が重要であることを学び、自主保全を実践してきました。
その後、TPM推進室でTPM継続賞から特別賞受賞までの事業所全体活動と、海外工場のTPM活動進捗と推進企画を行いました。また、製造課長として製造現場の管理・監督を経験後、資材部門にて協力会社の製造現場に入り込んで生産性改善によるコスト削減に取り組むほか、赤字海外工場に出向して製造現場の生産性改善による黒字化を達成しました。そして、鋳造会社の工場長を経て関係子会社2社の社長に就任し、新規工法の導入による生産品目の拡大と、既存製品の品質改善によるロス削減で黒字化を達成しました。
異動した先では必ずと言って良いほど、多くの不具合や大きな課題が残されていました。そのため、実行計画達成のためには、残された課題の改善と新規案件への挑戦と実行が必要でしたが、これまでの豊富な経験と改善することを楽しむ思考が、大きな力になったと思います。
◆問題解決の最も重要なプロセスは現状把握(現場、現物、現実)である
現在はコンサルタントとして、いろいろな工場の支援に当たらせていただいていますが、クライアント様からはこれまでの改善活動や自主保全について「活動が停滞している」「改善成果が出ない」といった声をいただきます。
しかし、そうした状況の多くについては現状把握と現状分析の不足が散見されます。なかには発生している問題自体を正確に把握できていないために間違った対策を取ったり、対策効果を正しく評価できていないにもかかわらず高度な分析手法に頼ったり安易な設備改善に進む傾向が見られます。
問題解決の最も重要なプロセスは、多くの方々がよく知っているQCストーリーの現状把握(現場、現物、現実)にあります。現品調査や発生事象ならびに不具合内容を細かく分類・層別することで、真の原因に辿りつけるケースが数多くあります。
改善活動は決して難しい活動ではありません。改善の基本を学び、改善を実践することで共に成長しましょう。
■竹内 康二プロフィール
◆専門分野: 工程改善支援
◆TPM:個別改善、自主保全、計画保全、品質保全、開発管理、教育訓練、管理間接、安全・衛生・環境
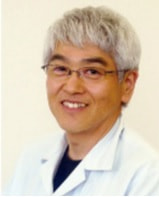